The Advantages of Automatic Loading and Unloading Systems in Modern Manufacturing
Introduction
In today’s fast-paced industrial landscape, automation has become a cornerstone of efficiency, safety, and cost-effectiveness. Among the most transformative innovations is the automatic loading and unloading system, particularly those integrated with laser technology. These systems streamline production processes, reduce human intervention, and enhance operational safety. A prime example is the laser loading and unloading robot, which enables more economical and secure manufacturing by automating material handling.
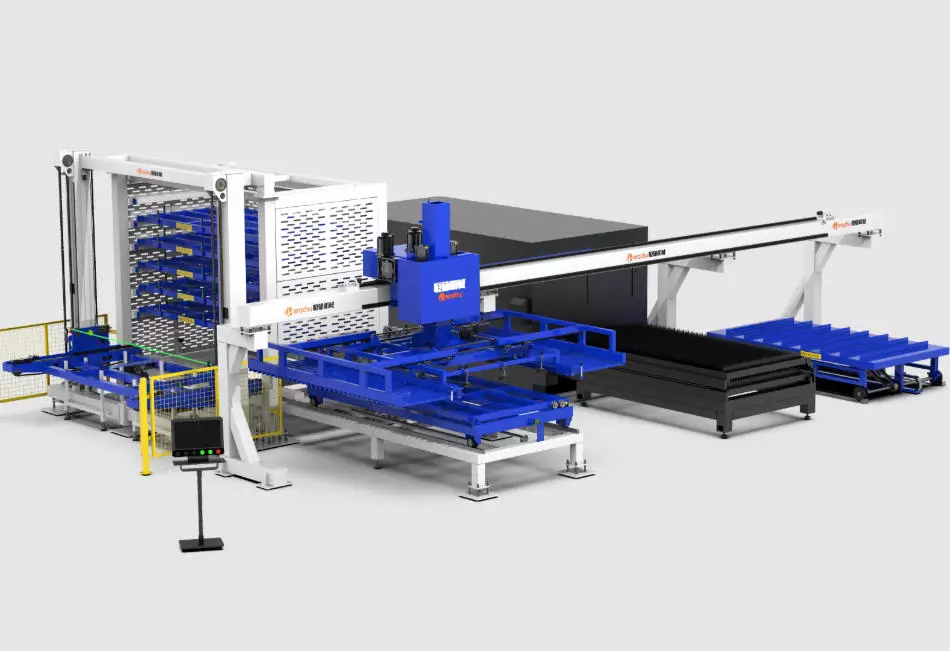
This article explores the components, benefits, and applications of automatic loading and unloading systems, with a focus on laser-based solutions. We will also examine how these systems contribute to smarter warehousing and production lines.
Components of an Automatic Loading and Unloading System
A fully automated loading and unloading system typically consists of the following key components:
The core of the system is the laser cutting machine, which performs precise cuts on various materials, including metal, plastic, and composites. By integrating an automated loading and unloading mechanism, the laser cutter can operate continuously without manual intervention, significantly improving productivity.
2. Laser Loading and Unloading Robot
The laser loading and unloading robot is designed to handle raw materials and finished products efficiently. Equipped with advanced sensors and grippers, these robots can:
Pick up raw materials and place them onto the laser cutting machine.
Remove processed parts and sort them for further operations.
Work seamlessly with other automated systems for uninterrupted production.
3. Electric Exchange Trolley
The electric exchange trolley facilitates the movement of materials between different stages of production. It ensures smooth transitions, minimizing downtime and optimizing workflow.
4. Linear Axis System
The loading and unloading device forms the most compact automation unit within the warehousing system through a linear axis. This setup allows for precise movement and positioning of materials, ensuring high-speed and accurate operations.

Key Benefits of Automatic Loading and Unloading Systems
1. Enhanced Efficiency and Productivity
Automated systems eliminate manual handling, reducing cycle times and increasing throughput. Since robots can work 24/7 without fatigue, production lines achieve higher efficiency.
2. Improved Safety
Manual loading and unloading of heavy or sharp materials pose significant risks. Automated systems minimize human involvement in hazardous tasks, reducing workplace injuries.
3. Cost Savings
While the initial investment may be substantial, automation leads to long-term savings by:
Reducing labor costs.
Minimizing material waste due to precision handling.
Lowering downtime through continuous operation.
4. Precision and Consistency
Robotic systems ensure consistent accuracy in material placement and removal, leading to higher-quality outputs with minimal errors.
5. Scalability and Flexibility
These systems can be adapted to various production environments, from small workshops to large-scale manufacturing plants. They can also be reprogrammed for different tasks, offering flexibility in operations.

Applications of Laser Loading and Unloading Systems
1. Metal Fabrication
In industries such as automotive and aerospace, laser cutting robots automate the handling of sheet metal, improving precision and reducing production time.
2. Warehousing and Logistics
Automated loading systems optimize storage and retrieval processes, making warehouses more efficient.
3. Electronics Manufacturing
Precision is critical in electronics production. Automated loading systems ensure delicate components are handled without damage.
4. Medical Device Production
Laser-based automation ensures sterile and accurate manufacturing of medical tools and implants.
Future Trends in Automated Loading and Unloading
As Industry 4.0 advances, we can expect:
AI-powered robots that learn and optimize workflows.
IoT integration for real-time monitoring and predictive maintenance.
Collaborative robots (cobots) working alongside humans for hybrid automation.
Conclusion
The automatic loading and unloading system, particularly those incorporating laser robots, represents a significant leap forward in manufacturing and warehousing. By enhancing efficiency, safety, and cost-effectiveness, these systems are becoming indispensable in modern industries. As technology evolves, we can anticipate even smarter, more adaptive automation solutions that will redefine production standards.
Investing in such systems today ensures businesses remain competitive in an increasingly automated world.
This article provides a comprehensive overview while maintaining originality and depth, suitable for a Google-friendly, SEO-optimized post. Let me know if you’d like any refinements!