Sheet Metal Vacuum Lifting Equipment: Enhancing Efficiency in Modern Manufacturing
In the fast-paced world of manufacturing, handling sheet metal—whether thin-walled car body panels, perforated sheets, or high-temperature formed parts—demands precision, speed, and reliability. This is where sheet metal vacuum lifting equipment emerges as a game-changer, revolutionizing automated processes with its unique blend of efficiency, adaptability, and cost-effectiveness.

At the core of sheet metal vacuum lifting equipment lies advanced vacuum technology, designed to make automated manufacturing processes more economical. Unlike traditional lifting methods, vacuum systems reduce energy consumption while boosting process speed and system availability. This dual benefit—lower operational costs and higher productivity—makes them indispensable for factories aiming to stay competitive in today’s market.
The unsung hero of these systems is the suction pad, engineered specifically for sheet metal handling. These pads boast high holding forces and exceptional lateral force absorption, enabling fast and secure handling of even the most delicate workpieces. What sets them apart is their specialized materials: formulated for sheet metal and metal applications, they offer outstanding ozone and oil resistance, preventing premature aging and extending service life. This durability directly translates to reduced maintenance needs and lower long-term costs for production plants.

Design innovation further elevates these suction pads. Their optimized structure allows seamless handling of workpieces with oiled surfaces—a common challenge in metalworking—without compromising grip. The bell-shaped design flexibly adapts to complex contours, from curved car body sheets to irregularly shaped laser-cut parts, ensuring a tight seal even on non-flat surfaces. Adding to their practicality, suction pads can be assembled or procured as individual components. This modularity simplifies replacements, reduces downtime, and cuts lifecycle costs, as plants can replace only worn parts instead of entire systems.
Sheet metal vacuum lifting equipment shines across a wide range of applications, proving its versatility in diverse manufacturing scenarios. For instance, it excels at handling narrow, elongated molded parts—think thin-walled car body sheets, tubes, or profiles—that are easily damaged by clumsy lifting. In CNC metalworking and laser cutting facilities, these systems streamline loading and unloading, minimizing machine idle time and maximizing throughput. They also play a critical role in destackers, efficiently handling blanks to keep production lines moving.
Beyond standard sheet metal, the equipment adapts to specialized needs. Magnetic grippers integrated with vacuum systems offer high holding forces for challenging workpieces: perforated sheets, complex laser-cut parts, and sheets with holes or cutouts. This versatility eliminates the need for multiple lifting tools, simplifying operations. Additionally, for high-temperature environments—such as hot forming processes—heat-resistant vacuum components ensure reliable performance, even when handling freshly formed, high-heat parts.
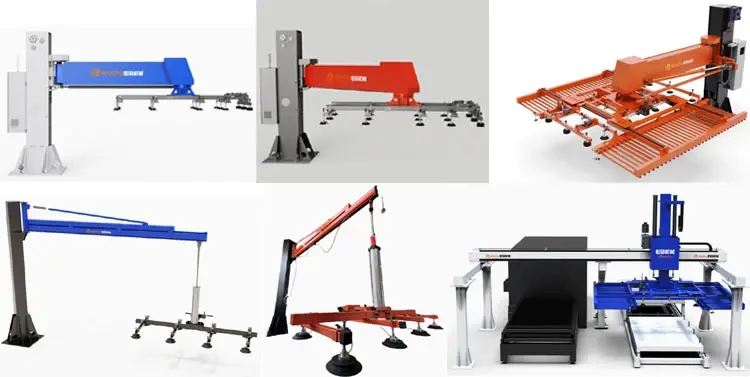
The impact of sheet metal vacuum lifting equipment extends beyond immediate efficiency gains. By reducing manual intervention, it lowers the risk of workplace injuries, enhancing safety. Its ability to handle delicate and irregularly shaped parts with precision reduces material waste, a key factor in sustainable manufacturing. Moreover, the system’s adaptability to oiled surfaces and complex contours means it integrates seamlessly into existing production lines, avoiding the need for costly reconfigurations.
In conclusion, sheet metal vacuum lifting equipment is more than a tool—it’s a strategic investment for modern manufacturing. Its combination of energy efficiency, adaptability, and durability addresses the unique challenges of sheet metal handling, from thin car body panels to high-temperature components. As factories continue to prioritize speed, cost reduction, and reliability, this technology will remain a cornerstone of efficient, automated production, driving innovation across industries.