Laser cutting machines have revolutionized modern manufacturing with their unmatched speed, precision, and efficiency, enabling fast-paced production lines across industries like automotive, aerospace, and metal fabrication. However, even the most advanced laser cutter can’t reach its full potential without a reliable loading and unloading system. As production demands grow, manual handling has become a bottleneck—slow, error-prone, and costly. This is where Herochu’s Loading and Unloading Systems for Laser Cutting Processes step in, designed to match the speed of laser technology and transform your workflow.

Why Loading and Unloading Systems Matter in Laser Cutting
Laser cutting machines operate at incredible speeds, slicing through metal sheets, tubes, and other materials with pinpoint accuracy. But without a streamlined way to load raw materials and unload finished parts, these machines spend too much time idle—waiting for operators to handle materials, adjust positions, or clear scrap. This downtime erodes productivity, increases labor costs, and limits the capacity to take on high-volume orders.
A high-performance loading and unloading system eliminates these issues. It ensures a continuous flow of materials into the laser cutter and removes finished products and scrap efficiently, keeping the machine running at peak performance. For manufacturers aiming to stay competitive, investing in the right system isn’t just an upgrade—it’s a necessity.
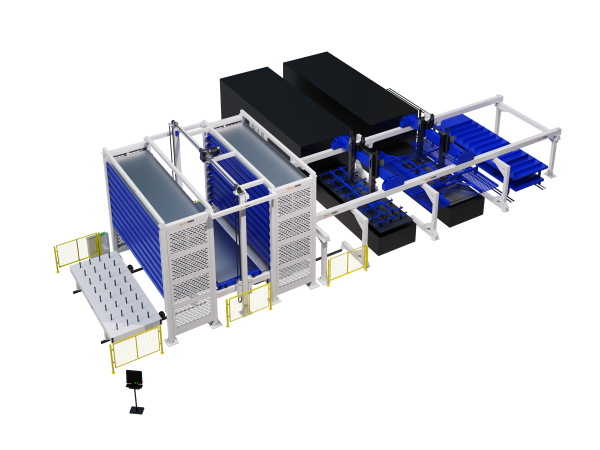
What Is a Loading and Unloading System for Laser Cutting?
A loading and unloading system for laser cutting is a specialized setup that manages the material flow before and after the cutting process. The loading system handles raw materials—such as metal sheets, tubes, or coils—by transporting them from storage to the laser cutter’s worktable, ensuring precise positioning for accurate cutting. The unloading system removes cut parts and scrap from the worktable, sorting them into designated areas to keep the workspace organized.
These systems can be manual, semi-automatic, or fully automatic, each suited to different production scales and needs. Herochu, a leader in industrial automation, offers a range of solutions tailored to optimize laser cutting workflows, from small workshops to large manufacturing facilities.
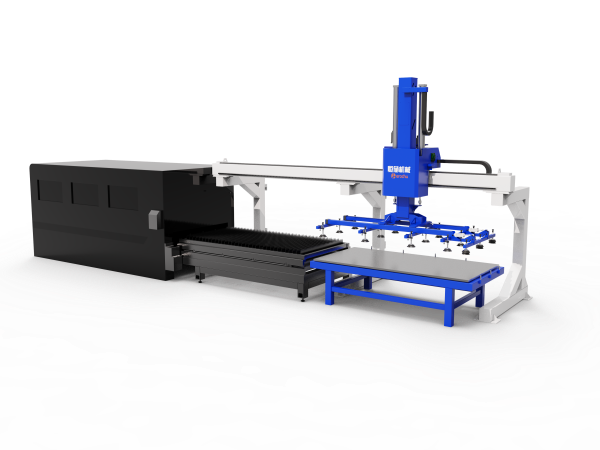
Types of Loading and Unloading Systems: Choosing the Right Fit
1. Manual Loading/Unloading: Traditional but Limited
Manual systems are the most basic option, relying entirely on operators to load raw materials and unload finished parts. Operators lift and position sheets or tubes onto the laser cutter, adjust their alignment, and remove cut pieces and scrap once the job is done.
Advantages:
- Lower initial cost: No investment in automated machinery, making it appealing for small businesses with tight budgets.
- Flexibility for irregular shapes: Operators can manually adjust materials with odd sizes or contours, which may be challenging for automated systems.
Disadvantages:
- High labor costs: Requires constant operator presence, increasing long-term expenses.
- Inconsistent precision: Human error in positioning can lead to cutting inaccuracies, reducing product quality.
- Downtime: Slow handling extends gaps between jobs, making it unsuitable for high-volume production.
Manual systems are fading in relevance as manufacturers prioritize speed and efficiency, but they may still work for tiny operations with low output.
2. Semi-Automatic Loading/Unloading: Balancing Automation and Control
Semi-automatic systems combine manual effort with automated features, striking a middle ground for businesses scaling up production. Operators load batches of raw materials (e.g., stacking sheets onto a feeder), while the system automatically positions them on the cutting bed. After cutting, the machine transfers finished parts to an unloading area, where operators sort and store them, sometimes with automated scrap collection.
Advantages:
- Improved productivity: Reduces manual handling time, allowing operators to manage multiple tasks simultaneously.
- Lower labor costs than manual systems: Less operator intervention cuts down on workforce needs.
- Reduced errors: Automated positioning ensures consistent alignment, 提升 cutting accuracy.
- Cost-effective: More affordable than fully automatic setups, making it ideal for medium-volume production.
Disadvantages:
- Still requires labor: Operators are needed for loading batches and unloading finished parts, limiting unattended operation.
- Less flexibility than manual systems: May struggle with highly irregular materials without operator adjustments.
Semi-automatic systems are a popular choice for businesses transitioning from manual processes but not yet ready for full automation.
3. Fully Automatic Loading/Unloading: The Gold Standard for High-Volume Production
Fully automatic systems, like those developed by Herochu, eliminate manual intervention entirely. These advanced setups handle every step—from loading raw materials to unloading finished parts and scrap—using robotics, vacuum lifters, conveyors, and smart software.
How do they work? Raw materials (sheets, tubes, or coils) are stored in organized stacks or pallets. Automated vehicles or robotic arms transport them to the laser cutter, where clamps or vacuum suction cups secure and position the material with micron-level precision. After cutting, the system sorts parts into designated areas, conveys scrap to waste bins, and reloads new materials—all without human input.
Advantages:
- 24/7 unattended operation: Runs continuously, even overnight or on weekends, maximizing machine uptime (often exceeding 85% for laser cutters).
- Unmatched speed: Handles materials at rates that outpace manual or semi-automatic systems, with fast transfer speeds reducing job gaps.
- Zero human error: Consistent positioning ensures every cut is precise, 提升 product quality and reducing waste.
- Lower long-term costs: Eliminates most labor expenses and reduces scrap, delivering a strong return on investment.
- Scalability: Easily integrates with other equipment (bending machines, coil fed systems) to create a fully automated production line.
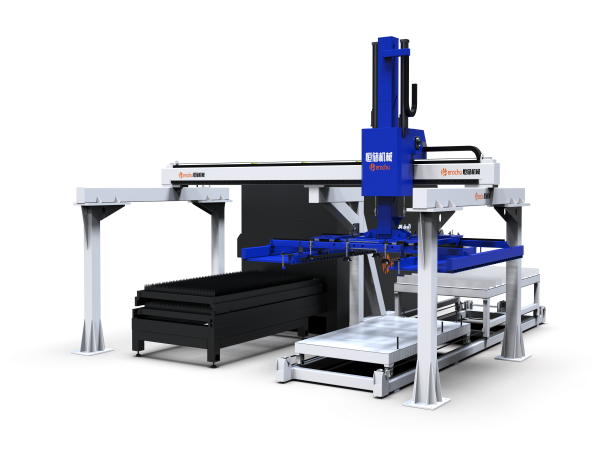
Why Herochu’s Automatic Systems Stand Out:
Herochu’s fully automatic loading and unloading systems are engineered for durability and efficiency. They feature:
- Vacuum lifters and robotic arms: Adapt to various material sizes (from thin sheets to thick plates up to 110mm) and shapes.
- Smart software integration: Syncs with laser cutters to optimize workflow, track inventory, and adjust schedules in real time.
- Safety features: Includes interlocking devices and sensors to prevent accidents, ensuring smooth operation even in busy factories.
- Flexible storage solutions: Movable sorting tables and pallet systems handle up to 5 tons, reducing congestion and streamlining post-cut processing.
Herochu: Your Partner in Laser Cutting Optimization
Whether you’re a small workshop or a large manufacturer, Herochu offers loading and unloading systems tailored to your needs. Their semi-automatic systems provide a cost-effective step toward automation, while their fully automatic solutions unlock 24/7 production, making them ideal for high-volume demands.
By choosing Herochu, you’re not just investing in machinery—you’re upgrading to a workflow that minimizes downtime, reduces costs, and delivers consistent quality. With their systems, laser cutters operate at full capacity, turning raw materials into finished parts faster than ever before.
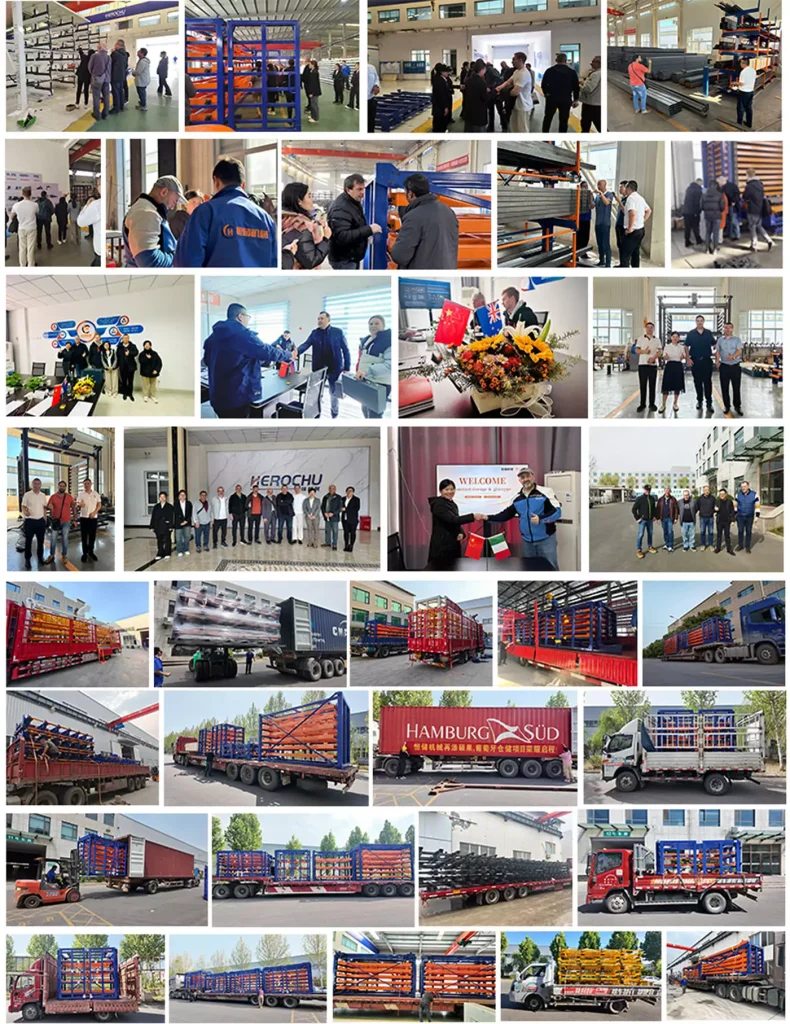
Conclusion: Choose the Right System for Your Goals
Loading and unloading systems are the unsung heroes of laser cutting efficiency. Manual systems work for tiny operations but hinder growth; semi-automatic setups balance cost and productivity; and fully automatic systems, like Herochu’s, are the future of high-volume manufacturing.
Ready to transform your laser cutting process? Explore Herochu’s loading and unloading systems today and discover how automation can boost your output, cut costs, and elevate your competitive edge in the market.