Introduction: The Critical Role of Automated Material Handling in Laser Cutting
In modern manufacturing, laser cutting machines are renowned for their speed, precision, and efficiency. However, their full potential can only be realized when paired with an optimized loading and unloading system. Manual material handling slows down production, increases labor costs, and introduces safety risks—making automation essential for competitive manufacturers.
Herochu’s Loading and Unloading Systems revolutionize laser cutting operations by enabling:
- Fully automated material feeding & part removal
- 24/7 unmanned production capabilities
- Seamless integration with existing laser cutters
- Smart sorting of finished parts and scrap
This comprehensive guide explores different types of loading/unloading systems, their benefits and drawbacks, and why automation is the future of laser cutting efficiency.

What Are Loading and Unloading Systems in Laser Cutting?
A Loading and Unloading System consists of equipment that:
- Feeds raw materials (sheets, tubes, etc.) into the laser cutter
- Positions them accurately for cutting
- Removes finished parts and scrap after processing
These systems can be:
- Manual (operator-dependent)
- Semi-automatic (partial automation)
- Fully automatic (robotized handling)
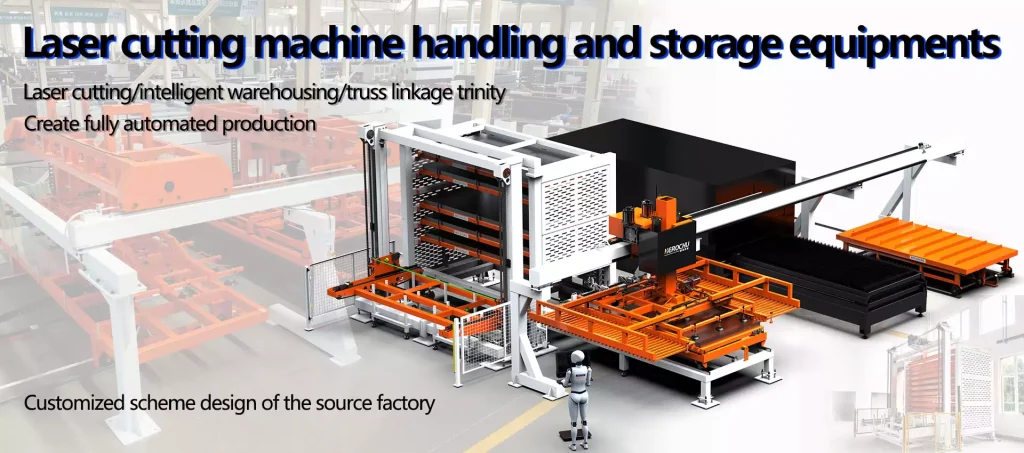
Types of Laser Cutting Loading/Unloading Systems
1. Manual Loading & Unloading System
How It Works
- An operator physically lifts and positions raw materials on the cutting bed
- After cutting, they manually remove parts and separate scrap
- Requires constant supervision
Advantages
✔ Lower upfront cost (no automation investment)
✔ Flexibility for irregular shapes or custom jobs
Disadvantages
❌ High labor costs (requires full-time operators)
❌ Slow processing (downtime between jobs)
❌ Human error risks (misalignment, accidents)
❌ Not scalable for high-volume production
Best for: Small workshops with low production demands
2. Semi-Automatic Loading & Unloading System
How It Works
- Operator loads multiple sheets at once into a feeder
- Automated positioning aligns material for cutting
- Conveyor or robotic arm removes finished parts
- Partial operator supervision required
Advantages
✔ Faster than manual systems
✔ Reduced labor costs (less operator involvement)
✔ Improved precision (automated alignment)
Disadvantages
❌ Still requires some manual intervention
❌ Higher initial cost than manual systems
❌ Limited continuous operation
Best for: Mid-volume production needing flexibility
3. Fully Automatic Loading & Unloading System
How It Works
- Robotic arms, suction cups, or conveyor belts feed materials
- Automated CNC positioning ensures perfect alignment
- AI-powered sorting separates finished parts from scrap
- Zero operator intervention needed
Advantages
✔ True 24/7 production (unmanned operation)
✔ Maximum efficiency (85%+ machine uptime)
✔ Highest precision (eliminates human error)
✔ Lowest labor costs (fully autonomous)
✔ Smart material management (auto-stacking, sorting)
Disadvantages
❌ Higher initial investment
❌ Requires proper integration
Best for: High-volume manufacturers needing maximum productivity
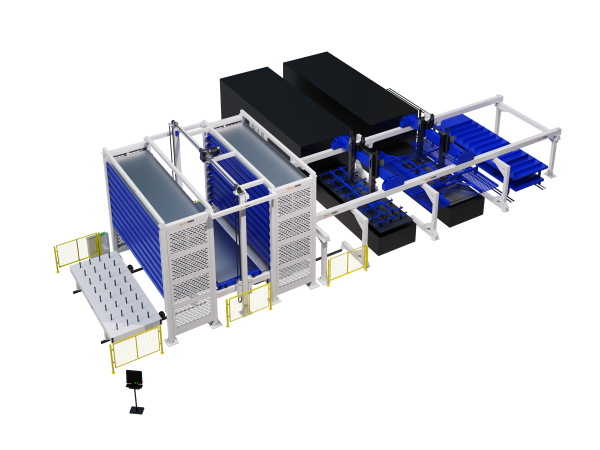
Why Automated Loading/Unloading is the Future
1. Unmatched Production Speed
- Eliminates downtime between jobs
- Continuous material feeding keeps lasers cutting non-stop
- 20+ cutting hours/day vs. 8-10 with manual systems
2. Dramatic Cost Reduction
- 60-80% labor savings vs. manual handling
- Minimized material waste from precise positioning
- Higher ROI from increased machine utilization
3. Enhanced Safety & Reliability
- No operator exposure to moving parts/lasers
- Fail-safe sensors prevent collisions
- Auto-error recovery maintains production flow
4. Smart Factory Integration
- Compatible with Industry 4.0 (IoT monitoring, predictive maintenance)
- Works with bending machines, coil feeders, etc.
- Centralized production control via PLC/HMI
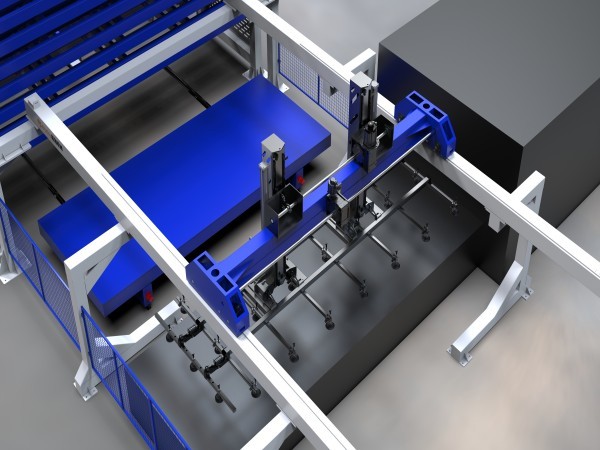
Herochu’s Advanced Automated Solutions
Key Features
- Heavy-duty material handling (up to 110mm thickness)
- Vacuum suction & fork systems for sheets/tubes
- 5-ton sorting tables for efficient scrap management
- Auto/Manual mode switching for flexibility
Technical Specifications
Parameter | Specification |
---|---|
Material Capacity | Sheets, tubes, plates (0.5-110mm) |
Automation Level | Fully unmanned operation |
Loading Speed | Up to 12m/min |
Sorting Capacity | 5-ton double-layer tables |
Integration | Laser cutters, benders, presses |

Industries That Benefit Most
- Automotive & aerospace (high-precision parts)
- Metal fabrication (mass production)
- Construction (structural components)
- Shipbuilding (thick-plate cutting)
Conclusion: Upgrade to Automated Efficiency Today!
Manual loading belongs in the past. Herochu’s Automated Loading/Unloading Systems deliver:
✅ 30-50% faster production cycles
✅ 85%+ machine uptime
✅ Labor-free 24/7 operation
✅ Seamless smart factory integration
Contact Herochu now to transform your laser cutting workflow!
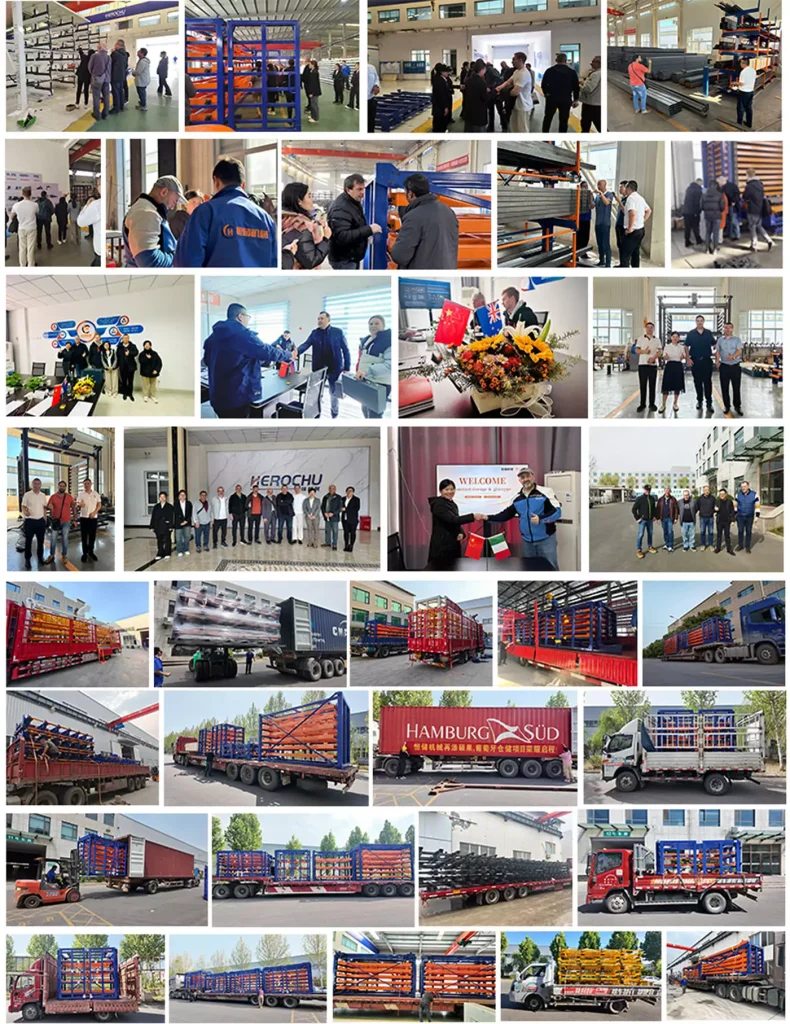