In the realm of metal fabrication and manufacturing, the smooth operation of sheet metal storage warehouses relies heavily on efficient loading and unloading processes. The integration of advanced loading and unloading systems with smart sheet metal storage solutions has become a cornerstone of modern industrial productivity. These systems not only streamline material handling but also enhance safety, reduce downtime, and maximize space utilization—critical factors for businesses aiming to stay competitive in a fast-paced market.

The Core Components of a Sheet Metal Storage and Handling System
A state-of-the-art sheet metal storage warehouse system is a synergy of several key components, each designed to work in harmony to ensure seamless loading and unloading. At its core is the three-dimensional storage material warehouse, a space-saving structure that allows vertical storage of sheet metal, significantly increasing storage density compared to traditional horizontal racks. Complementing this is the double-sided gantry truss, which provides a stable framework for the movement of handling equipment, enabling precise positioning across the warehouse.
For loading operations, the suction cup type loading manipulator takes center stage. Equipped with powerful, heavy-duty suction cups, it securely grips various sheet metal types—from aluminum to stainless steel—without causing damage. This is particularly crucial for maintaining the integrity of delicate or coated sheets. On the unloading side, the fork type unloading manipulator efficiently transfers sheets from storage to processing areas or transport vehicles, handling heavier loads with ease.
The system also includes a double-layer electric exchange material car, which facilitates the transfer of sheets between different parts of the warehouse, reducing the need for manual intervention. Controlling all these components is a CNC control system, ensuring precise coordination of movements, while the vacuum control system regulates the suction force of the loading manipulator, adapting to different sheet thicknesses and weights. Together, these components create a fully integrated solution that minimizes human error and maximizes operational efficiency.
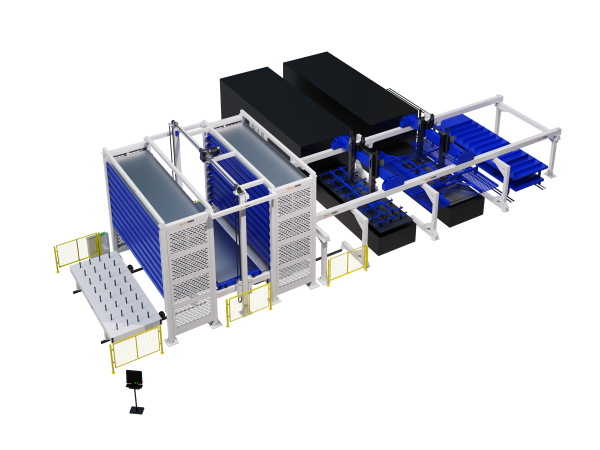
Key Specifications: Tailored to Handle Diverse Sheet Metal Needs
Sheet metal storage and handling systems are designed with versatility in mind, offering specifications that cater to a wide range of industrial requirements. The systems accommodate sheet sizes of 3015mm, 4015mm, and 4020mm, making them suitable for standard and large-format sheets commonly used in fabrication.
When it comes to load capacity, the systems are built to handle heavy-duty operations. Each layer of the three-dimensional storage warehouse can support up to 3T, with a maximum load per sheet ranging from 100KG to 500KG—ideal for everything from thin gauge aluminum to thick carbon steel sheets. The skip load (the capacity of the material transfer car) is also 3T, ensuring that even large batches of sheets can be moved efficiently within the warehouse.
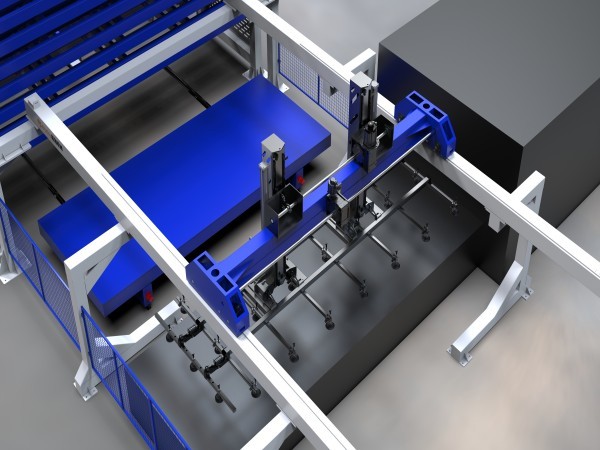
Pneumatic performance is another critical specification. The system operates with an air consumption of 1.5m³/min, providing sufficient power to the suction cup manipulators and other pneumatic components. This ensures reliable gripping and release of sheets during loading and unloading, even in high-volume, continuous operation scenarios.
Advantages of Integrating Loading/Unloading Systems with Sheet Metal Storage
The integration of advanced loading and unloading systems with sheet metal storage warehouses offers a multitude of benefits for industrial operations:
- Space Optimization: The three-dimensional storage design, combined with automated handling equipment, maximizes vertical space utilization. This is especially valuable in warehouses with limited floor area, allowing businesses to store more sheets without expanding their facility.
- Enhanced Efficiency: Manual loading and unloading of sheet metal are not only labor-intensive but also slow and prone to delays. Automated systems reduce the time spent on these tasks by enabling rapid retrieval and storage. Operators can quickly locate and transfer sheets using the CNC control system, cutting down on downtime and increasing overall throughput.
- Improved Safety: Sheet metal, particularly large or heavy sheets, poses significant safety risks when handled manually. The risk of strains, injuries, or sheet damage is drastically reduced with suction cup and fork type manipulators. These tools are designed to grip sheets securely, preventing slips and falls, while the gantry truss system ensures stable movement across the warehouse.
- Superior Material Protection: Sheet metal is susceptible to scratches, dents, or corrosion if not handled properly. The suction cup loading manipulator uses controlled vacuum pressure to grip sheets without applying excessive force, preserving their surface quality. Additionally, the organized storage in the three-dimensional warehouse prevents sheets from rubbing against each other, maintaining their integrity until they are ready for use.
- Scalability and Adaptability: The modular design of these systems allows for easy customization. Whether a warehouse needs to add more storage layers (ranging from 8 to 13 floors) or adjust the handling equipment to accommodate new sheet sizes, the system can be modified to meet evolving needs. This adaptability makes it a long-term investment that grows with the business.
Applications Across Industries
Sheet metal storage warehouses equipped with advanced loading and unloading systems are indispensable in various sectors:
- Metal Fabrication Shops: These facilities handle a constant flow of sheet metal for cutting, bending, and welding. The system ensures that raw materials are quickly loaded into processing machines and finished products are stored efficiently, reducing bottlenecks in production.
- Automotive Manufacturing: Automakers rely on large volumes of sheet metal for body panels, chassis components, and structural parts. The system’s ability to handle heavy loads and diverse sheet sizes makes it ideal for managing the high throughput of automotive production lines.
- Aerospace and Defense: Precision is paramount in these industries, where sheet metal must meet strict quality standards. The gentle handling provided by suction cup manipulators ensures that delicate or high-value sheets (such as aluminum alloys used in aircraft) remain undamaged.
- Construction and Architecture: From stainless steel cladding to carbon steel beams, construction projects require various sheet metal types. The warehouse system keeps these materials organized and accessible, ensuring timely delivery to job sites.
Why Invest in a Sheet Metal Storage Warehouse with Automated Loading/Unloading?
The decision to implement an advanced sheet metal storage and handling system is a strategic one, with benefits that extend beyond immediate operational improvements. By reducing labor costs associated with manual handling, minimizing material waste due to damage, and increasing storage capacity, businesses can achieve significant cost savings over time.
Moreover, the CNC control system provides valuable data insights, such as inventory levels, usage patterns, and equipment performance. This data helps managers make informed decisions about stock replenishment, maintenance schedules, and workflow optimization, further enhancing efficiency.
In an industry where precision and speed are critical, the combination of loading and unloading automation with a smart sheet metal storage warehouse is no longer a luxury—it’s a necessity. It empowers businesses to meet tight deadlines, maintain high product quality, and adapt to changing market demands with ease.
Conclusion
The integration of efficient loading and unloading processes with a well-designed sheet metal storage warehouse is transformative for industrial operations. By leveraging components like three-dimensional storage, gantry trusses, and automated manipulators, businesses can achieve unprecedented levels of efficiency, safety, and space utilization.
Whether handling small batches of specialty sheets or large volumes of standard materials, these systems deliver consistent performance that enhances productivity and reduces operational costs. For any organization involved in metalworking, investing in such a system is a step toward a more competitive, agile, and profitable future.