In the realm of modern manufacturing, laser cutting has become indispensable for its precision and speed in processing sheet metal and other materials. However, the efficiency of laser cutting operations often hinges on the loading and unloading processes—manual handling can slow down production, increase labor costs, and introduce safety risks. Herochu’s laser loading unloading system addresses these challenges, offering a fully automated solution that transforms how industries handle material transfer in laser cutting workflows. Designed for economy, safety, and precision, this system is a game-changer for facilities seeking to optimize their laser cutting operations.

At the heart of Herochu’s offering is its automatic loading and unloading system, which leverages advanced laser loading and unloading robots to streamline production. These robots eliminate the need for manual material handling, enabling more economical and safer manufacturing processes. By automating repetitive loading and unloading tasks, the system reduces human error, minimizes workplace accidents, and allows workers to focus on more skilled operations—ultimately boosting overall productivity. Whether handling small precision parts or large sheet metal panels, Herochu’s robots deliver consistent performance, ensuring seamless material flow throughout the production cycle.
Herochu’s laser loading unloading system is engineered as a compact automation unit, integrating seamlessly with existing warehousing setups. The system’s core components include a laser cutting machine, a laser loading and unloading robot, and an electric exchange trolley, all connected via a linear axis that optimizes space usage. This compact design is particularly valuable for facilities with limited floor space, as it eliminates the need for bulky, separate automation equipment. The linear axis ensures smooth, precise movement of materials between stations, reducing transfer time and maximizing the efficiency of the entire production line.

The loading manipulator is a standout feature of Herochu’s system, built for durability and reliability. Welded from high-strength square tube, it boasts the structural integrity to handle heavy loads with ease. Equipped with vacuum suction cups, the manipulator securely grips plates during transfer, ensuring stable handling even for large or irregularly shaped materials. A key innovation is the plate layer thickness measurement device, which prevents the common issue of loading multiple plates at once during feeding. This technology eliminates jams, reduces material waste, and ensures that only the correct number of plates enter the laser cutting machine—saving time and maintaining consistent quality.
Herochu’s laser loading unloading system is built on a foundation of stability and precision, starting with its truss fuselage. Designed for stable performance, the truss structure minimizes vibration during operation, ensuring accurate material positioning. Its user-friendly design also makes installation and debugging straightforward, reducing downtime during setup and allowing facilities to start benefiting from automation quickly. This combination of stability and ease of use makes the system suitable for both experienced manufacturing teams and those new to automated solutions.

Control and precision are further enhanced by the system’s PLC controller and servo drive technology. The PLC (Programmable Logic Controller) serves as the system’s brain, running independent, custom-developed software that coordinates all operations—from robot movement to material detection. This ensures seamless synchronization between the loading/unloading robot, laser cutting machine, and electric exchange trolley. Paired with servo drive technology, the system achieves high precision in every movement, with exact positioning that eliminates errors in material alignment. This level of precision is critical for maintaining the accuracy of laser cutting operations, ensuring that finished parts meet strict quality standards.
Automated operation is a defining advantage of Herochu’s system, enabling unmanned working cycles that maximize the utilization rate of the laser cutting machine. With the ability to run continuously without manual intervention, the system significantly increases production output, even during off-hours or shifts with limited staffing. This 24/7 operational capability is a major driver of cost savings, as it reduces labor expenses while boosting throughput. Additionally, the system’s roller table positioning feature minimizes the time spent on edge searching, further accelerating the cutting process and reducing cycle times.
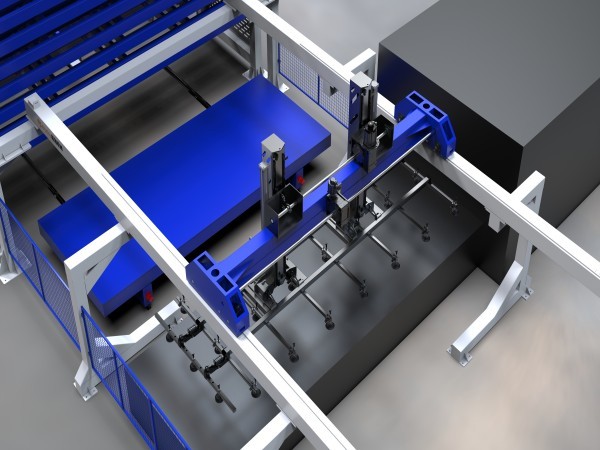
For facilities looking to scale their operations, Herochu’s laser loading unloading system offers expandable capabilities through optional storage units. By integrating a whole set of storage units, the production cycle becomes more optimized, with materials pre-staged for immediate loading and finished parts automatically stored for later retrieval. This creates a fully automated material flow from storage to cutting to final storage, eliminating bottlenecks and ensuring a continuous production loop.
In industries where precision, efficiency, and safety are paramount, Herochu’s laser loading unloading system stands out as an essential investment. Its combination of compact design, durable construction, advanced sensing technology, and automated operation transforms laser cutting operations, reducing costs and increasing productivity. By choosing Herochu, manufacturers gain a reliable partner in automation—one that delivers the precision and efficiency needed to stay competitive in today’s fast-paced manufacturing landscape.