In the realm of metal fabrication, laser cutting has become synonymous with precision and speed—but even the most advanced laser cutter is only as efficient as its material handling process. Manual loading and unloading of sheets not only slows production but also introduces risks of errors and workplace injuries. Enter the laser cutting machine automatic loading and unloading warehouse, with the full-automatic one-to-two loading and unloading double-tower plate system standing out as a transformative solution. Designed to streamline every step of the process, this system turns fragmented workflows into seamless, fully automated production lines.
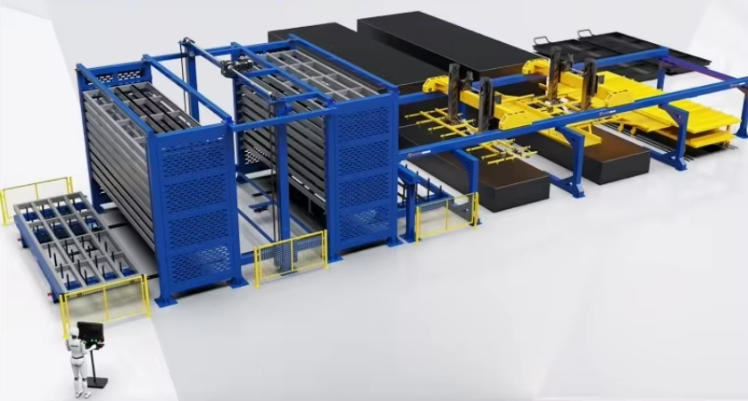
At its core, the full-automatic one-to-two double-tower warehouse redefines efficiency by handling multiple tasks without human intervention: automatic sheet separation, feeding, blanking, and even coordination with laser cutting machines. This all-in-one automation eliminates bottlenecks, reduces downtime, and ensures consistent output—critical for high-volume manufacturing environments. Unlike single-tower systems, the “one-to-two” design enables the warehouse to serve two laser cutting machines simultaneously, doubling throughput without doubling manual effort.
Customization is a key strength, with specifications tailored to diverse production needs. The system accommodates sheet sizes ranging from 3×1.5m and 4×1.5m to 4x2m, with full customization options for unique requirements. Layer counts are equally flexible, offering 8-13 layers (and beyond, upon request), while per-layer load capacities reach 3T or 5T, supporting total loads from 300KG to 3000KG. This adaptability makes it ideal for industries handling everything from thin gauge sheets to heavy-duty metal plates.
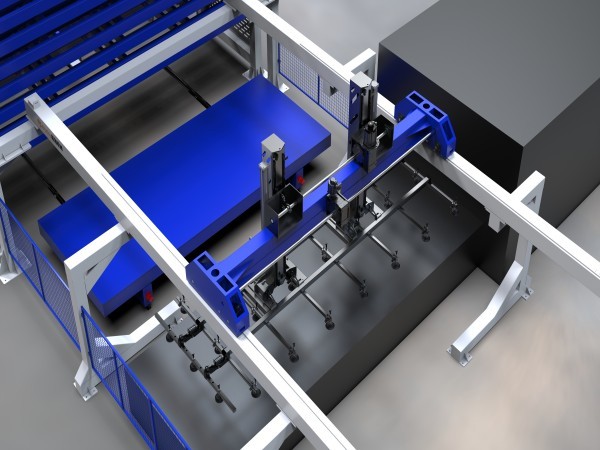
The system’s power lies in its integrated components, working in harmony to deliver uninterrupted production. A three-dimensional storage warehouse serves as the central hub, organizing raw materials and finished parts with optimal space efficiency. Flanking this are bilateral gantry trusses, providing stable rails for the loading and unloading truss manipulators—each dedicated to feeding raw sheets into laser cutters or retrieving finished parts. A double-layer finished material truck collects cut pieces, keeping the workflow moving without congestion. At the heart of it all is a PLC control system, orchestrating every movement with precision, and linking seamlessly with laser cutting machines to form a cohesive automatic production unit.
User-centric design ensures operators retain control without sacrificing automation. Near each laser machine, an operation box allows quick switching between the two machines for automatic feeding, adapting to shifting production priorities. The touchscreen interface simplifies toggling between automatic and manual feeding modes, catering to scenarios where hands-on adjustment is needed—such as handling irregularly shaped sheets or troubleshooting. This flexibility ensures the system thrives in both high-volume runs and custom, low-batch projects.
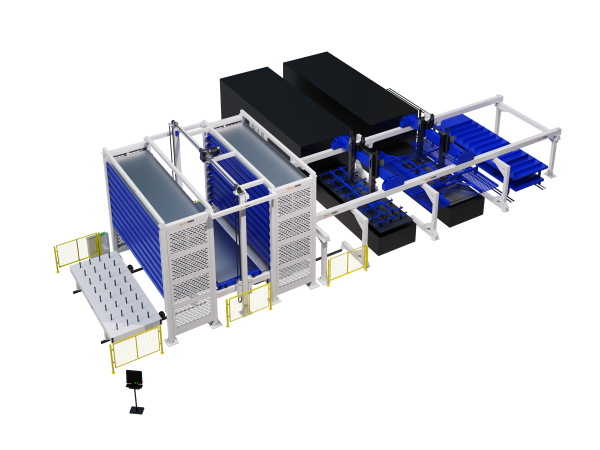
The manipulators themselves are engineering marvels, designed for versatility and precision. Equipped with a pneumatic rotating structure, they rotate sheets 90 degrees effortlessly, adapting to both transverse and longitudinal feeding requirements—eliminating the need for pre-orientation of materials. Driven by high-speed variable frequency motors, their movements are swift yet controlled, boasting fast running speeds and high repeated positioning accuracy (often within millimeters), critical for aligning sheets with laser cutting beds.
Gripping is handled by a vacuum suction cup system, featuring trusted brand components for unwavering reliability. Each suction cup’s relative position is adjustable within a range, ensuring a secure grip on sheets of varying sizes. With independent control switches for each cup, operators can activate only the necessary ones via the controller—optimizing suction force for thin or small sheets and reducing energy use. This targeted gripping minimizes sheet deformation, preserving material integrity and cutting precision.
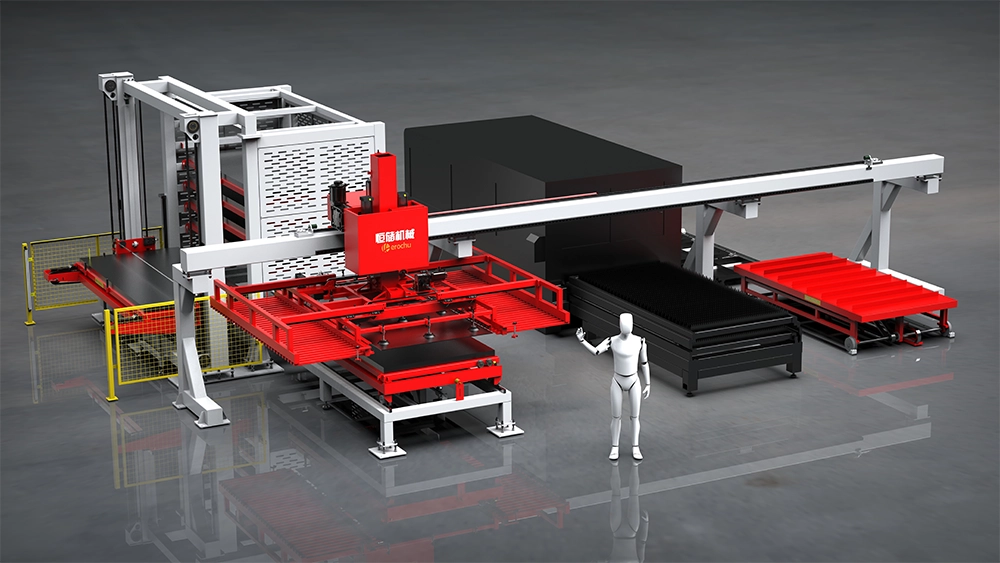
Safety is woven into every detail. The vacuum system’s redundancy and independent cup controls prevent accidental drops, while the PLC’s real-time monitoring ensures all components work in sync—halting operations if anomalies are detected. This focus on safety reduces material waste and protects workers from heavy lifting or pinch hazards.
In conclusion, the laser cutting machine automatic loading and unloading warehouse—especially the full-automatic one-to-two double-tower system—represents the future of metal fabrication. By merging full automation with customization, user-friendly controls, and precision engineering, it transforms laser cutting operations from labor-intensive processes to streamlined, high-efficiency lines. Whether handling large-scale production or custom projects, this system delivers faster turnaround, lower costs, and safer workplaces—making it an indispensable asset for manufacturers aiming to stay competitive in today’s fast-paced industrial landscape.