In the fast-evolving landscape of sheet metal fabrication, the laser cutting loading machine has become a cornerstone of efficient and automated production. This advanced system combines key components to form a seamless sheet metal automatic production unit, including a unilateral gantry truss, loading and unloading composite truss manipulator, double-layer finished material truck, PLC control system, and a laser cutting machine. Together, these elements redefine productivity, safety, and cost-effectiveness in modern manufacturing.
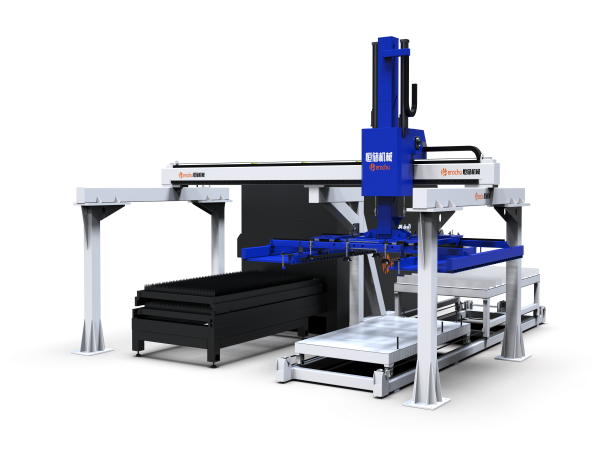
Core Components and System Integration
The laser cutting loading machine’s strength lies in its well-engineered components working in perfect harmony. The unilateral gantry truss provides a stable and precise movement framework, enabling the system to navigate the workspace with accuracy. Paired with it is the loading and unloading composite truss manipulator, which handles material gripping, lifting, and placement—eliminating the need for manual intervention.
The double-layer finished material truck adds versatility by offering separate storage spaces for different types of cut parts, optimizing post-cutting organization. At the center of operations is the PLC control system, which synchronizes all components, ensuring smooth transitions between loading, cutting, and unloading phases. When integrated with the laser cutting machine, this setup creates a closed-loop production system that minimizes delays and maximizes output.

Technical Specifications for Versatile Performance
The laser cutting loading machine is designed to adapt to diverse production needs, as highlighted by its technical parameters. It supports multiple specifications, including 3015mm, 4015mm, 4020mm, and 4025mm, making it suitable for processing various sheet sizes commonly used in industries like automotive, aerospace, and construction.
In terms of load capacity, the system offers a maximum load range of 100KG to 500KG, accommodating both light and medium-gauge metal sheets. The skip load—capable of handling up to 3T—ensures that even heavy batches of materials or finished products can be transported efficiently within the production line.
For reliable operation, the machine requires an air consumption of 1.5m³/min and an air source pressure of 0.6-0.7Mpa. These pneumatic requirements are optimized for industrial settings, ensuring consistent performance and quick response times during high-volume production runs.

Key Functions: Automation and Safety
One of the primary advantages of the laser cutting loading machine is its ability to automate loading and unloading processes through laser loading and unloading robots. These robots follow preset instructions to handle materials, reducing the risk of human error and workplace accidents associated with manual lifting of heavy sheets. By minimizing direct worker contact with machinery and sharp materials, the system enhances on-site safety—a critical factor for compliance with modern labor regulations.
The automation extends beyond basic material handling. The loading and unloading device, paired with a linear axis, forms the most compact automation unit of the warehousing system. This space-efficient design is ideal for factories with limited floor space, as it eliminates the need for bulky manual handling equipment. Additionally, the system can include an electric exchange trolley, which further streamlines material transfer between the storage area and the laser cutting machine, ensuring a continuous workflow.
Economic Benefits of Automated Production
Implementing a laser cutting loading machine translates to significant cost savings for manufacturers. By automating loading and unloading, businesses reduce their reliance on manual labor, cutting down on workforce expenses. The consistent and precise handling of materials also minimizes waste—scrap metal from misaligned cuts or damaged sheets is drastically reduced, lowering material costs over time.
Moreover, the system’s efficiency leads to higher production throughput. With minimal downtime between cycles, more sheets can be processed in a given period, accelerating order fulfillment and enabling businesses to take on larger projects. This increased productivity directly contributes to higher revenue and a stronger competitive edge in the market.
Seamless Integration with Manufacturing Ecosystems
The laser cutting loading machine is designed to integrate effortlessly with existing manufacturing systems, making it a flexible addition to any production line. Its compatibility with warehouse management systems (WMS) and manufacturing execution systems (MES) allows for real-time tracking of materials, from loading to finished product storage. This connectivity ensures that production schedules are optimized, and inventory levels are managed efficiently.
The compact automation unit formed by the loading and unloading device also simplifies integration with other equipment. Whether paired with standalone laser cutters or part of a larger automated warehouse, the system adapts to different layouts without requiring extensive reconfiguration. This versatility makes it a valuable investment for both small-scale workshops and large industrial facilities.
Conclusion: A Smart Choice for Modern Fabrication
In summary, the laser cutting loading machine represents a significant leap forward in sheet metal production automation. Its combination of robust components, versatile technical specifications, and automated functions delivers a solution that enhances safety, improves efficiency, and reduces costs. By handling loading, unloading, and material transfer with precision, it allows manufacturers to focus on quality control and process optimization rather than manual labor.
For businesses looking to stay ahead in the competitive world of sheet metal fabrication, investing in a laser cutting loading machine is a strategic decision. It not only meets the demands of high-volume production but also aligns with the industry’s shift toward smart manufacturing—where automation, connectivity, and efficiency are key to long-term success.