Herochu Fiber Laser Robot Arm & Sheet Metal Plate Rack: CE-UE-ISO 9001-Certified High-Performance Automation
When European design philosophy meets Asian manufacturing precision, the result is the Herochu integrated system—pairing a six-axis Fiber Laser Robot Arm with a heavy-duty Sheet Metal Plate Rack—engineered for 24/7 lights-out production in the most demanding sheet-metal environments. CE, UE and ISO 9001 certifications validate every weld, wire and line of code, guaranteeing global compliance and repeatable quality.
European-Inspired Gantry Architecture
The heart of the solution is a gantry-loading manipulator whose overhead bridge eliminates floor obstacles and maximizes usable workspace. A high-torque servo synchronous lifting mechanism positions the robot arm within ±0.05 mm, while servo translation drives deliver rapid traverse speeds up to 120 m/min across the full 4020 mm X-axis envelope. The rigid, stress-relieved gantry beam is modeled on German DIN 18800 standards for fatigue resistance, ensuring micron-level path accuracy during high-dynamic laser cuts.
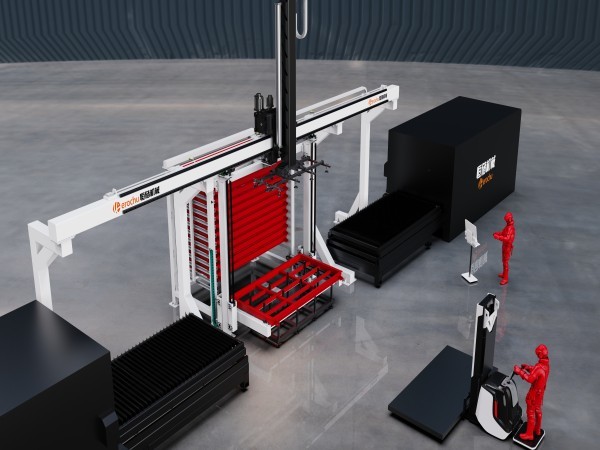
Intelligent Sheet Metal Plate Rack
Flanking the robot is Herochu’s five-tier automatic storage and discharge rack. Each level supports 3 t of distributed load, giving a cumulative capacity of 15 t while still permitting single-sheet retrieval. A modular roll-out drawer system—protected by oil-resistant, heavy-duty vacuum suction cups—handles 100 kg–500 kg plates without edge deformation . Linear rails and zero-backlash rack-and-pinion drives deliver ±0.1 mm repeatability, allowing the robot to pick the top sheet in under 15 s. Drawer dimensions are available in 3015, 4015 and 4020 mm to match common laser bed sizes .
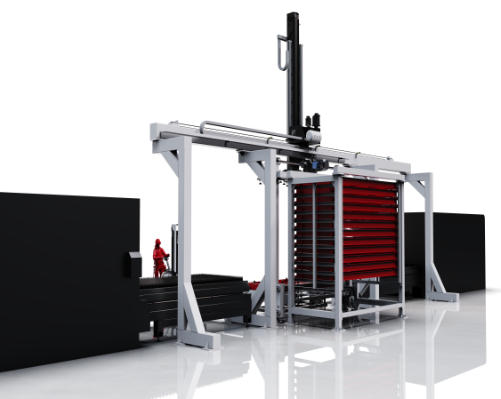
Omron CNC & SNS Pneumatics
The entire cell is orchestrated by an original Omron NJ-series CNC paired with the Sysmac Studio environment. EtherCAT fieldbus synchronizes the robot, gantry axes and rack actuators within 1 ms, eliminating micro-lag that can compromise cut quality. A Japanese SNS pneumatic circuit supplies 0.6–0.7 MPa oil-free air at 1.5 m³/min, powering both vacuum generation and sheet-separation blow-off nozzles. Real-time pressure feedback prevents double-sheet pickup and reduces idle energy by 18 %.
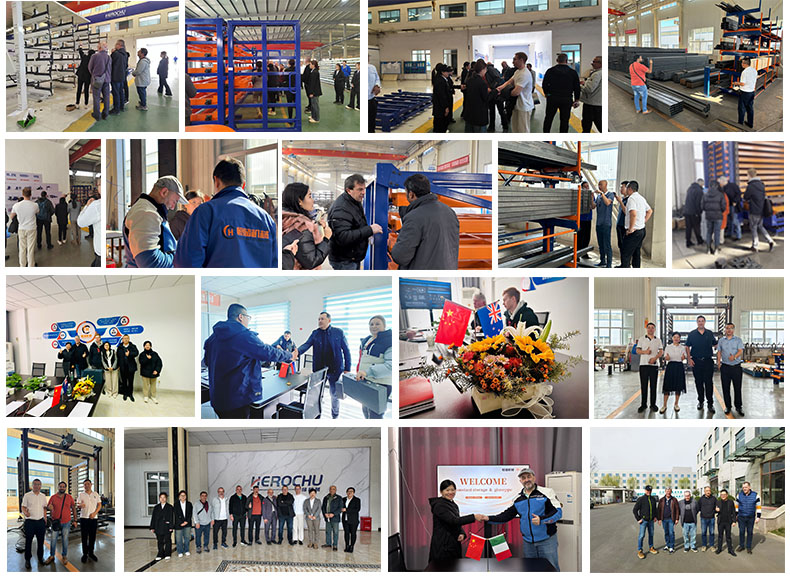
Safety & Maintenance by Design
Category-4 safety PL e light curtains surround the load/unload zone, while SIL-3 interlocks disable laser emission the instant a human breach is detected. All service points are reachable from floor level; hinged side panels expose the servo drives and pneumatic manifold without crane assistance. Mean Time To Repair (MTTR) is <30 min thanks to hot-swappable vacuum cartridges and plug-and-play cable sets.
Performance Snapshot
• Working envelope: 4020 × 2020 mm (optional 3015/4015)
• Z-axis stroke: 300 mm, 0.01 mm resolution
• Maximum plate thickness: 25 mm carbon steel, 15 mm aluminum
• Rack load per layer: 3 t; total floors: 5
• Suction cup array: 8-zone independent control; oil-resistant NBR foam rated to 120 °C
• Air consumption: 1.5 m³/min @ 0.65 MPa; integrated booster eliminates external compressor upgrade
• Certifications: CE Machinery Directive 2006/42/EC, UE EMC 2014/30/EU, ISO 9001:2015
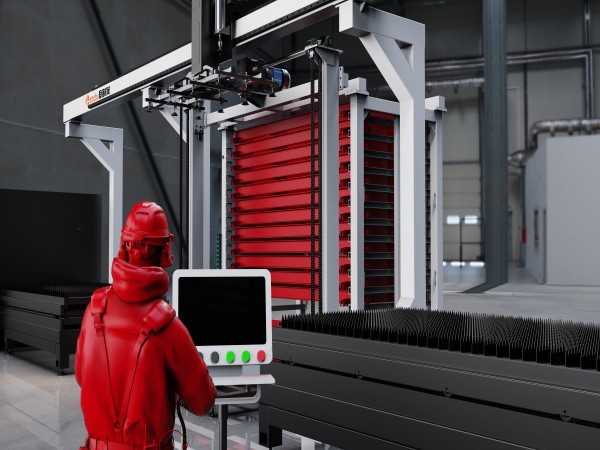
ROI in Real Numbers
Field data from a Tier-1 elevator manufacturer show 37 % higher throughput versus manual loading, 92 % reduction in surface scratching, and payback in 14 months on three-shift operation. The modular drawer system also enabled a 28 % floor-space saving compared with traditional cantilever racks .
Future-Proof Scalability
Need to double capacity next year? Additional rack bays bolt directly to the existing frame and auto-register through the Omron network. The Fiber Laser Robot Arm firmware is OTA-updatable, ensuring compatibility with tomorrow’s process innovations.
Herochu delivers more than equipment; it delivers a certified, data-driven path to unmanned sheet-metal productivity.