The Critical Role of Automated Storage in Modern Laser Cutting Operations
In today’s high-volume manufacturing environment, laser cutting machines have become astonishingly productive – but this creates a new challenge. As fiber laser technology advances, with cutting speeds now exceeding 100 meters per minute for thin sheets, the bottleneck has shifted from cutting capacity to material handling. Herochu’s Automatic Storage Systems solve this fundamental production constraint by creating seamless material flow from raw sheet storage through to finished part management.
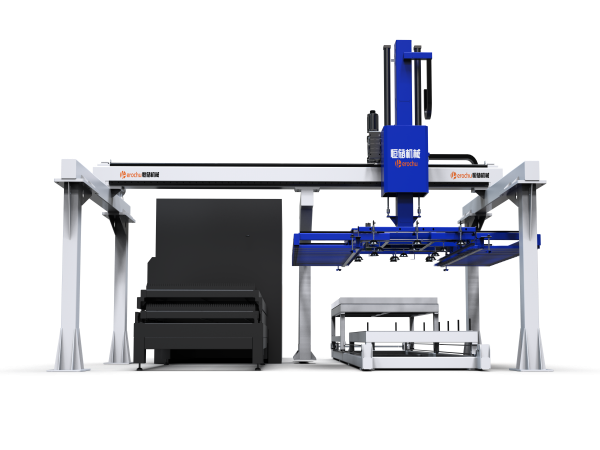
Why Automated Storage is No Longer Optional
The Productivity Paradox of Modern Laser Cutters
Modern 10kW+ fiber lasers can process:
- 3-5x faster than older CO₂ machines
- 24/7 operation with proper automation
- Thousands of parts daily from single sheets
Yet most facilities still rely on:
- Manual forklift loading (5-10 minutes per sheet)
- Disorganized scrap management
- Labor-intensive part sorting
This mismatch means lasers sit idle 30-50% of the time waiting for materials.
Three Critical Flow Challenges Automated Storage Solves
- Raw Material Supply
- Managing 50+ material grades/thicknesses
- Minimizing sheet separation time (especially for thin gauges)
- Eliminating forklift traffic near machines
- Cut Part Organization
- Preventing nested part mix-ups
- Protecting finished part quality
- Enabling just-in-time sorting
- Scrap Management
- Automating remnant storage
- Tracking reusable offcuts
- Optimizing material yield
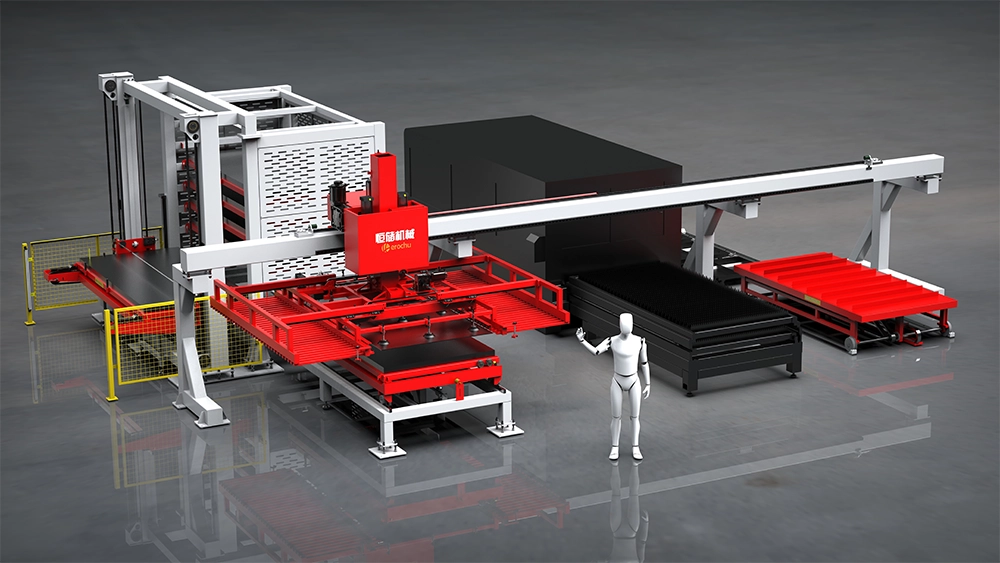
Herochu’s Automated Storage Solutions
1. Storage Tower Systems
- Vertical raw material buffers (8-12m height)
- 3T-5T capacity per shelf
- Barcode/RFID tracking
- Automatic sheet separation
- Direct machine integration
Typical Results:
- 90% reduction in material loading time
- 60% less floor space vs horizontal storage
- 24-hour raw material buffer
2. Cut Part Sorting Systems
- Robotic part picking with vision systems
- Automated palletizing by job/order
- Protected storage until next operation
- MES/ERP integration for traceability
3. Smart Scrap Management
- Automated remnant storage
- AI-powered nesting optimization
- Real-time material tracking
- Salvage value reporting
Key Benefits of Automated Laser Storage
1. Eliminate Machine Downtime
- Continuous material supply matches laser speed
- No more waiting for forklift loading
- 85%+ machine utilization achievable
2. Optimize Labor Productivity
- 1 operator can manage multiple machines
- Eliminate non-value-added material handling
- Reduce fatigue-related errors
3. Maximize Material Yield
- Automated remnant management
- Smart nesting recommendations
- 5-15% material savings
4. Improve Quality Control
- No manual sheet handling damage
- Protected finished part storage
- Perfect job traceability
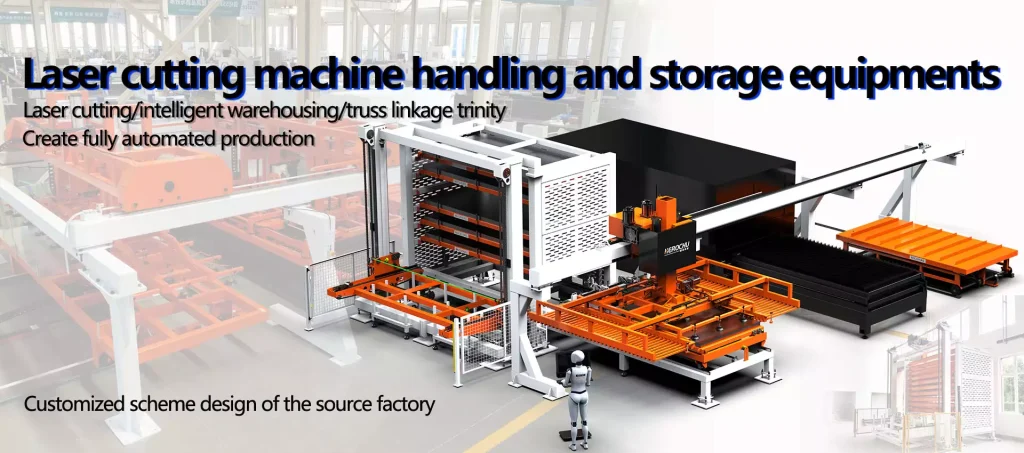
Implementation Roadmap
1. Data Collection & Analysis
- Material usage patterns
- Current handling time studies
- Bottleneck identification
2. System Sizing
- Raw material buffer capacity
- Cut part storage needs
- Scrap handling requirements
3. Phased Integration
- Raw material automation
- Cut part handling
- Scrap management
- Full MES integration
Industry-Specific Applications
Automotive Tier Suppliers
- High-volume blanking
- Just-in-sequence part delivery
- Multi-material handling
Metal Service Centers
- 50+ material grades
- Custom blank production
- Remnant resale value
HVAC & Electrical Enclosures
- Mixed thickness processing
- Job-specific sorting
- High part variety
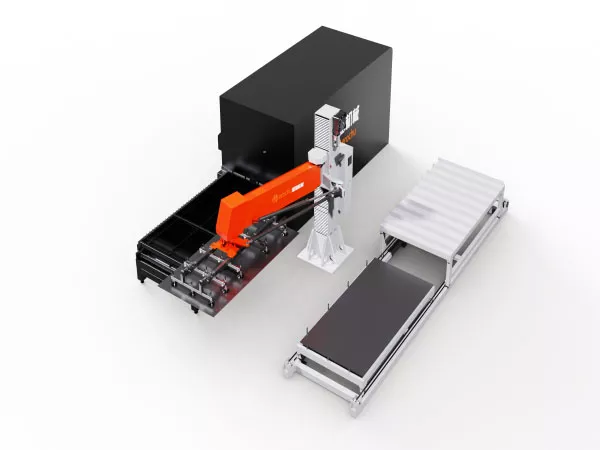
Conclusion: The Future is Automated
As laser cutting speeds continue increasing, automated storage systems transition from luxury to necessity. Herochu’s solutions deliver:
✅ 30-50% productivity gains
✅ 20-30% labor savings
✅ 5-15% material optimization
✅ 100% traceability
Contact our material flow experts today for a free facility assessment!