In the realm of sheet metal fabrication, the productivity of laser cutting machines hinges not just on their cutting speed or precision, but on the efficiency of material flow—from raw sheet metal entering the factory to cut parts exiting the laser station. With the rise of high-power fiber laser sources, modern laser cutters now produce parts at unprecedented rates, creating a critical need: continuous, seamless loading and unloading to keep up with this output. Herochu’s Automatic Loading and Unloading System for Laser Cutting Machines is engineered to bridge this gap, transforming chaotic material flows into streamlined, data-driven processes that elevate factory productivity and organization.
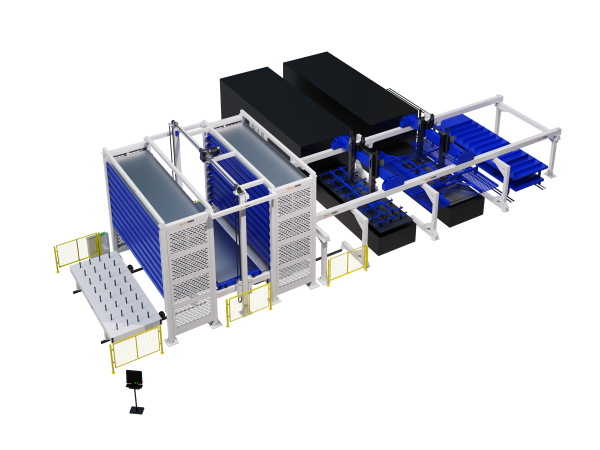
The Need for Automation: Matching High-Power Laser Output
Today’s high-power fiber lasers have redefined production capacity. These machines slice through thin to medium-thickness sheets with 惊人的 speed, often requiring loading or unloading cycles every few minutes to avoid idle time. Manual handling—relying on forklifts, operators, and manual sheet positioning—simply can’t keep pace. Delays in feeding raw materials or removing cut parts create bottlenecks, wasting the laser’s potential and dragging down overall efficiency.
Herochu’s automatic system solves this by synchronizing with the laser cutter’s rhythm. It ensures raw sheets are loaded precisely when needed and cut parts are unloaded instantly, keeping the laser running at peak capacity. For factories processing high volumes of thin or medium-thickness sheets, this continuous operation is a game-changer, turning underutilized laser power into tangible output gains.
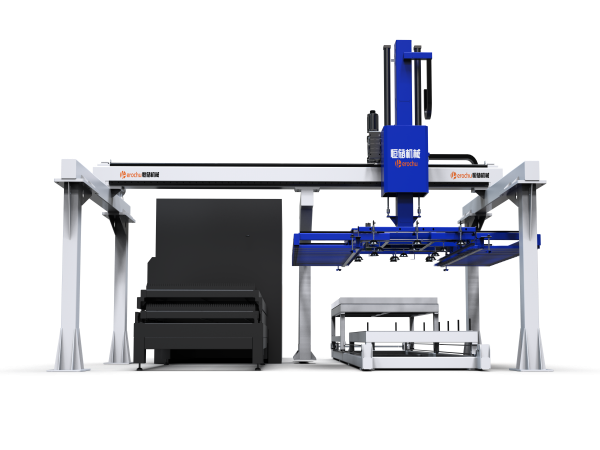
Starting at the Source: The Cutting Station as a Flow Hub
In sheet metal factories, the laser cutting station is typically the first production step, making it the ideal starting point to optimize material flow. Herochu’s system treats this station as a central hub, managing both incoming raw materials and outgoing cut parts. By structuring flows here, it creates a ripple effect—improving downstream processes like bending, welding, or assembly, where disorganized cut parts often cause delays.
This holistic approach eliminates siloed storage and handling, ensuring raw materials move smoothly into the laser, and cut parts transition seamlessly to the next stage. Whether parts are sorted immediately or stored for later processing, the system maintains visibility and control, reducing errors and lost inventory.
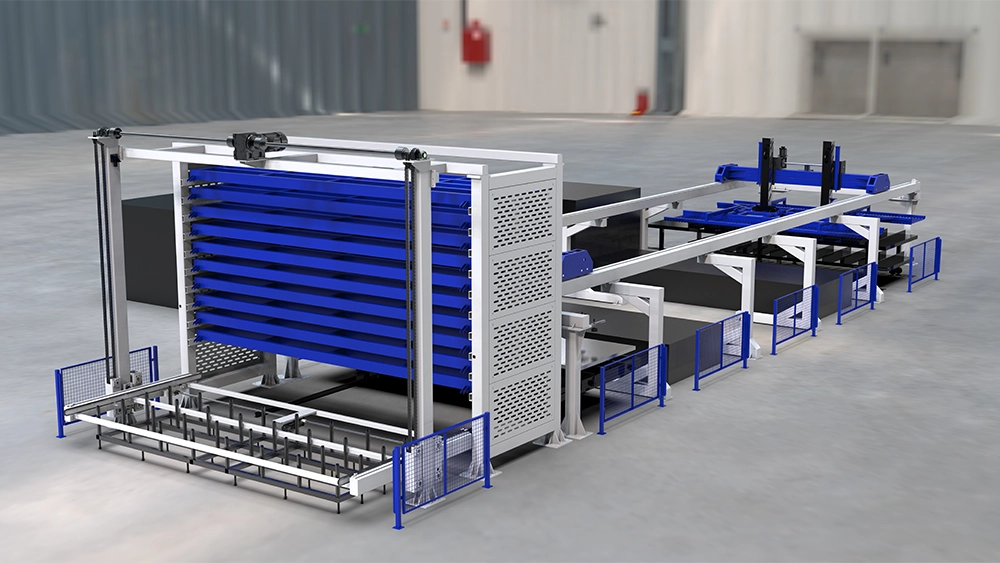
Data-Driven Sizing: Building a System That Fits Your Needs
Investing in automation requires understanding your unique workflow—and Herochu emphasizes data collection to tailor its system. Key data points include:
- Material references: Identifying the 80% of sheet grades, thicknesses, and sizes that drive 80% of production, ensuring the system prioritizes these for quick access.
- Manual handling steps: Mapping tasks like forklift operation, pallet extraction, sheet counting, and machine loading reveals hidden time sinks. Herochu’s system automates these steps, cutting handling time by up to 70%.
- Pain points: Difficulties like separating thin sheets, scrap from mishandling, or safety risks during transport are addressed with features like vacuum lifters (for easy sheet separation) and guided rails (for safe movement).
- Time and downtime metrics: Measuring average manual loading time (often 15–20 minutes per cycle) and laser idle time (due to material delays) quantifies the system’s ROI. Herochu’s clients typically see a 30%+ reduction in laser downtime.
This data ensures the system is sized correctly—avoiding overinvestment in unnecessary capacity or underpowered solutions that fail to meet demand.
Raw Material Management: From Storage to Laser, Seamlessly
Supplying laser cutters with raw materials is rife with challenges: managing diverse sheet types, moving heavy stacks, and repurposing offcuts. Herochu’s system addresses each:
- Diverse inventory handling: The system accommodates various grades (mild steel, aluminum, stainless), thicknesses, and sizes (up to 6020mm), with customizable storage towers that organize sheets by type for instant retrieval.
- Automated transport: Guided by sensors and software, raw sheets are moved from storage to the laser’s bed without operator intervention. Forklift reliance is minimized, reducing labor costs and accident risks.
- Offcut optimization: The system tracks and stores offcuts, making them easy to locate for small jobs, reducing material waste by up to 25%.
For many clients, Herochu’s storage towers are the cornerstone here. These vertical structures maximize floor space while keeping high-demand sheets at eye level, ensuring the laser never waits for material.
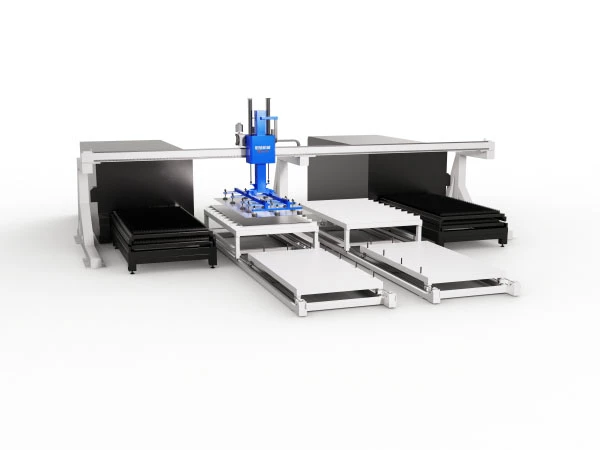
Managing Cut Parts: Flexibility for Every Workflow
Once cutting is complete, Herochu’s system adapts to how you process parts:
- Batch storage: Cut sheets are temporarily stored in towers for later sorting, ideal for high-volume runs where immediate sorting isn’t feasible.
- Instant sorting: Robotic arms (integrated with the system) or operators sort parts onto pallets, with the system logging each part’s location for quick retrieval in downstream steps.
This flexibility ensures the system aligns with your workflow, whether you prioritize speed, labor savings, or downstream processing needs.
Beyond the Laser: Scalability for Growing Demand
Herochu’s Automatic Loading and Unloading System isn’t just a laser accessory—it’s a scalable solution. As production grows, the system expands: adding storage layers, integrating with additional lasers, or connecting to MES/ERP systems for end-to-end data tracking. This scalability future-proofs your investment, ensuring it evolves with your factory’s needs.
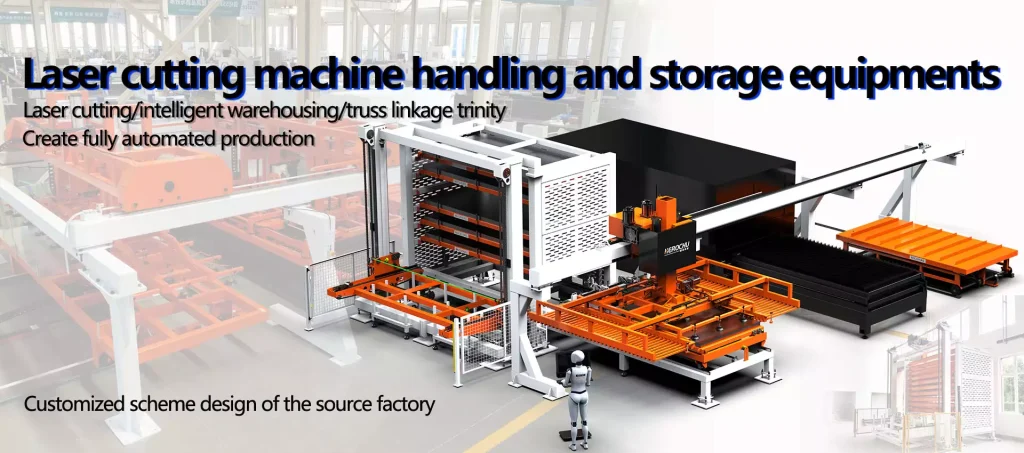
Why Herochu?
Herochu’s system stands out for its focus on real-world workflow integration. Unlike generic automation tools, it’s designed specifically for laser cutting environments, with features like:
- Adaptive speed: Syncs with laser cutter cycles to avoid bottlenecks.
- Durable construction: Handles heavy sheets (up to 5T per layer) with precision.
- User-friendly software: Simplifies inventory tracking, order scheduling, and system monitoring, even for non-technical staff.
By combining data-driven design, seamless flow management, and scalability, Herochu transforms the laser cutting station from a productivity bottleneck into a competitive advantage.
Conclusion: Elevate Your Laser Cutting Efficiency
In a market where speed and precision determine success, Herochu’s Automatic Loading and Unloading System for Laser Cutting Machines is more than an upgrade—it’s a necessity. It ensures your high-power laser lives up to its potential, reduces labor costs, minimizes errors, and creates a foundation for smarter, more profitable manufacturing.
Ready to streamline your material flows? Contact Herochu to build a system tailored to your laser cutting needs.