In the realm of metal fabrication and industrial manufacturing, the Fiber laser cutting machine stands as a cornerstone of precision and speed. Yet, even the most advanced laser cutter can underperform if bogged down by inefficient material handling. This is where the Automatic Loading and Unloading System emerges as a transformative solution, engineered to maximize productive time by ensuring an uninterrupted material flow—turning potential downtime into valuable output.
At its core, this system is a dynamic combination loading and unloading device, designed with two key mechanisms that work in perfect sync: suction cups for loading raw materials and rakes for removing finished sheets. The suction cups, often equipped with adjustable pressure settings, securely grip various materials—from thin metal sheets to thicker alloys—without causing deformation. This precision ensures raw materials are positioned accurately on the laser cutter’s bed, eliminating alignment errors that could compromise cut quality. On the flip side, the rakes come into play post-cutting: they gently but firmly lift and transport finished sheets away from the work area, preventing scratches or damage to the newly cut edges. This dual-action design streamlines the transition between loading and unloading, creating a seamless loop that keeps the laser cutter in constant operation.
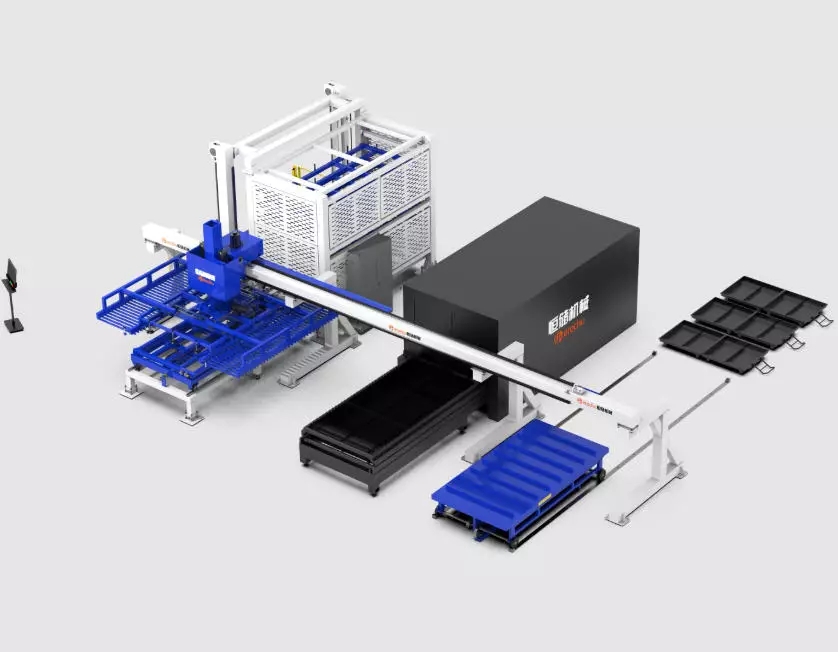
One of the system’s most compelling advantages is its fast material exchange time. In traditional setups, operators spend precious minutes manually swapping out raw sheets for finished ones, leading to frequent pauses in laser cutting. With the automatic system, these delays vanish. The transition from unloading a completed sheet to loading a new one happens in seconds, meaning the laser cutter rarely waits idle for the next material. For high-volume production facilities, this translates to hours of recovered productivity each week—directly impacting the bottom line by increasing the number of parts or sheets processed daily.
Beyond speed, the system’s automatic operation unlocks a game-changing capability: long periods of unmanned operation. Once programmed, the system can run independently through night shifts, weekends, or during breaks, with minimal oversight. This is a boon for manufacturers facing labor shortages or looking to maximize output without increasing staffing costs. Imagine a facility where the laser cutter continues slicing through metal sheets while the shop floor is empty—turning idle hours into profitable production. This level of autonomy also reduces human error, as there’s no risk of manual misalignment or mishandling of materials, ensuring consistent quality across every cut.
Another standout feature is the system’s scalability, particularly when paired with a Herochu material storage system. While the base automatic loading and unloading setup optimizes material flow, adding a Herochu storage system extends its capabilities by increasing on-site material capacity. This integrated storage solution can hold large quantities of raw sheets—from aluminum to stainless steel—organizing them in a compact, accessible structure. The automatic system communicates seamlessly with the storage unit, retrieving new materials as needed and sending finished products to designated storage bays. For manufacturers dealing with diverse material types or large batch sizes, this means less time spent on inventory management and more time focused on cutting.
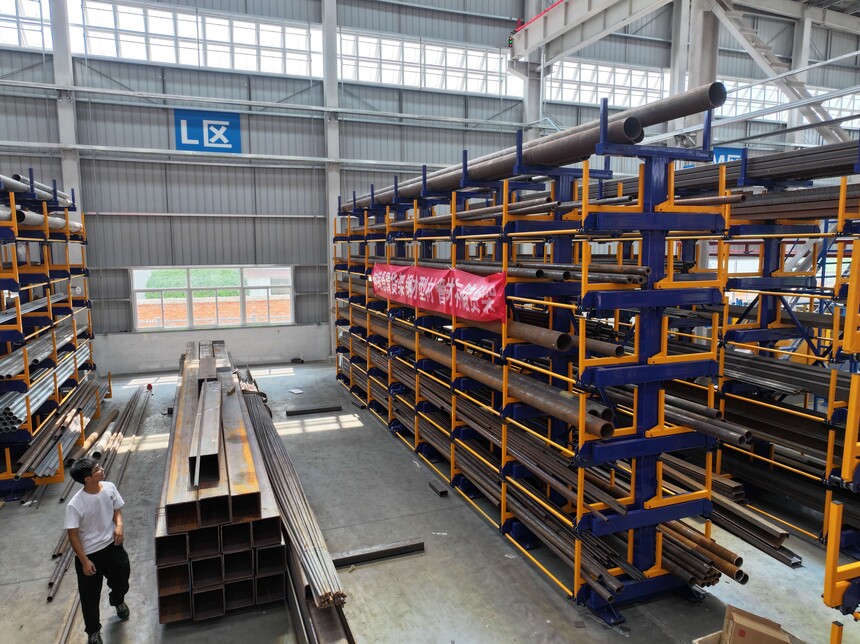
The benefits of this synergy ripple through the entire production chain. Reduced downtime lowers per-unit production costs, as fixed expenses like energy and equipment depreciation are spread across more output. Consistent material handling improves quality control, minimizing waste from misaligned cuts or damaged sheets. Meanwhile, the ability to operate unmanned frees up skilled workers to focus on more complex tasks—such as programming the laser cutter or inspecting finished products—enhancing overall operational efficiency.
In industries where deadlines are tight and margins are thin, the Automatic Loading and Unloading System is more than a convenience—it’s a strategic investment. By ensuring Fiber laser cutting machines run at peak capacity, eliminating waiting times, and enabling extended unmanned operation, it transforms how manufacturers approach productivity. Paired with a Herochu storage system, it becomes a comprehensive solution that grows with business needs, proving that in modern manufacturing, efficiency isn’t just about speed—it’s about keeping the workflow moving, without interruption.