In modern manufacturing and metalworking industries, efficient storage and handling of sheet metal are critical for maintaining productivity and minimizing operational delays. An automated loading and unloading system integrated with a sheet metal storage warehouse provides a smart, space-saving, and high-capacity solution for factories, fabrication shops, and warehouses.
This advanced system combines three-dimensional storage, robotic manipulators, and intelligent CNC control to optimize material flow, reduce manual labor, and enhance workplace safety. With load capacities up to 3T per layer and modular configurations, it is ideal for industries dealing with aluminum, stainless steel, carbon steel, and other sheet metals.
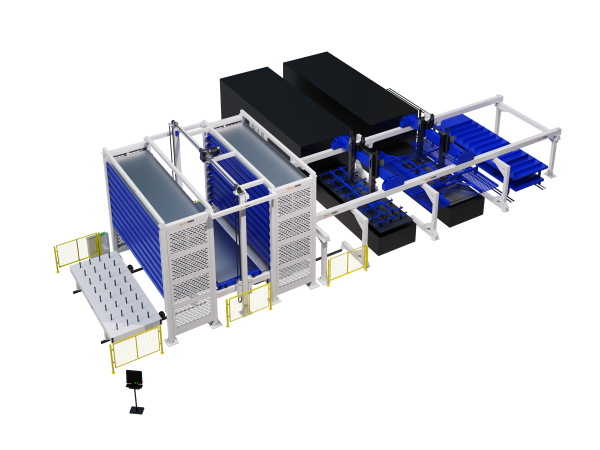
Key Components of the Automated Sheet Metal Storage System
1. Three-Dimensional Storage Material Warehouse
The core of the system is a high-density storage warehouse designed to maximize vertical space utilization.
- 8-13 floors of storage capacity
- Load per layer: 3T (expandable based on requirements)
- Compact footprint for efficient use of warehouse space
- Modular design for easy expansion
2. Double-Sided Gantry Truss for Precision Handling
A heavy-duty gantry truss ensures smooth and accurate movement of sheet metal across the storage system.
- Dual-sided operation for simultaneous loading/unloading
- High rigidity structure for stability under heavy loads
- CNC-guided positioning for precise material placement
3. Robotic Manipulators for Automated Handling
The system features two specialized manipulators for seamless material transfer:
A. Suction Cup Loading Manipulator
- Vacuum-based gripping for secure handling of sheet metal
- Adjustable suction force to accommodate different material weights (100KG-500KG)
- Gentle material placement to prevent scratches or deformations
B. Fork-Type Unloading Manipulator
- Heavy-duty fork mechanism for lifting and transporting sheets
- 3T skip load capacity for high-efficiency operations
- Compatible with various sheet sizes (3015/4015/4020mm)
4. Double-Layer Electric Exchange Material Car
An automated transfer cart ensures smooth movement between storage and processing stations.
- Dual-layer design for simultaneous material exchange
- Electric-powered operation for energy efficiency
- Seamless integration with CNC machines
5. Intelligent Control Systems
The entire system is managed by advanced automation technologies:
- CNC Control System – Ensures precise coordination between components
- Vacuum Control System – Regulates suction force for optimal grip
- Automated Inventory Tracking – Real-time monitoring of stored materials
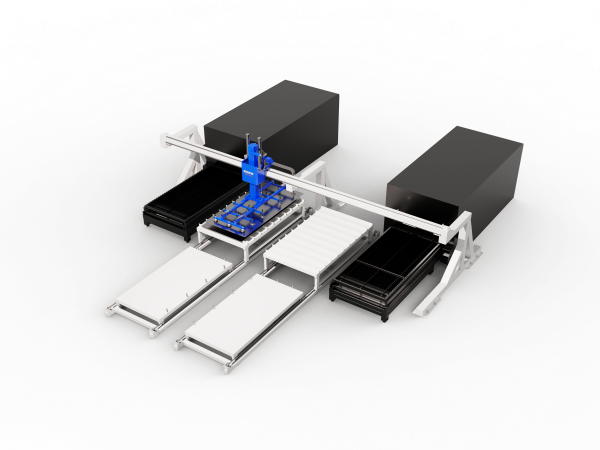
Benefits of an Automated Sheet Metal Storage System
1. Maximized Storage Efficiency
- Vertical storage reduces floor space usage by up to 70% compared to traditional racks.
- High-density organization minimizes clutter and improves accessibility.
2. Faster Material Handling & Reduced Downtime
- Automated loading/unloading speeds up retrieval by 3-5x compared to manual methods.
- Simultaneous operations (loading while unloading) enhance workflow efficiency.
3. Enhanced Material Protection
- Scratch-free handling with vacuum suction and soft-contact forks.
- Stable storage conditions prevent warping or damage.
4. Improved Workplace Safety
- Reduces manual lifting risks (ergonomic hazards).
- Automated safety protocols prevent accidents during operation.
5. Scalability & Customization
- Modular design allows expansion as storage needs grow.
- Configurable layouts to fit different factory floor plans.
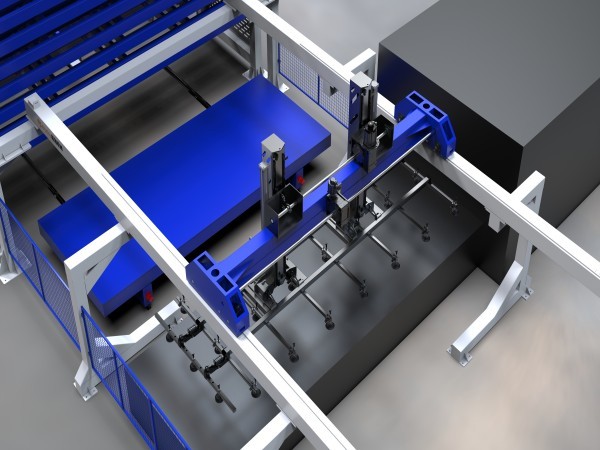
Applications Across Industries
1. Metal Fabrication & Stamping Plants
- Automated retrieval for laser cutting, bending, and punching machines.
- Just-in-time material supply for production lines.
2. Automotive Manufacturing
- Efficient storage of body panels, chassis parts, and stainless steel sheets.
- Seamless integration with robotic welding systems.
3. Aerospace & Defense
- Secure handling of high-value aluminum and titanium sheets.
- Traceability with automated inventory management.
4. Electronics & Appliances
- Precision handling of thin metal sheets for enclosures and components.
Technical Specifications
Feature | Specification |
---|---|
Storage Dimensions | 3015/4015/4020mm |
Number of Floors | 8-13 |
Load per Layer | 3T |
Max. Handling Capacity | 100KG-500KG (Manipulator) |
Skip Load Capacity | 3T |
Air Consumption | 1.5m³/min |
Control System | CNC Automation |
Why Choose an Automated Sheet Metal Storage System?
✅ Space Optimization – Store more in less space.
✅ Labor Savings – Reduce manual handling by 80%.
✅ Faster Operations – Minimize retrieval time.
✅ Damage Prevention – Protect high-value materials.
✅ Future-Ready – Easily upgradable for Industry 4.0 integration.
Conclusion
An automated loading and unloading system for sheet metal storage warehouses revolutionizes industrial material handling by increasing efficiency, reducing costs, and improving safety. With high-capacity storage, robotic manipulators, and intelligent control, this system is a must-have for modern metalworking facilities.
Upgrade your warehouse today and experience faster production cycles, better inventory control, and higher ROI with automated sheet metal storage!