Introduction to Laser Cutting Automation
In today’s fast-paced manufacturing environment, automation has become crucial for maintaining competitive edge in sheet metal fabrication. The cantilever manipulator for laser cutting represents a breakthrough in material handling technology, designed to streamline production, enhance precision, and reduce labor costs. This comprehensive guide explores how this innovative system revolutionizes laser cutting operations.
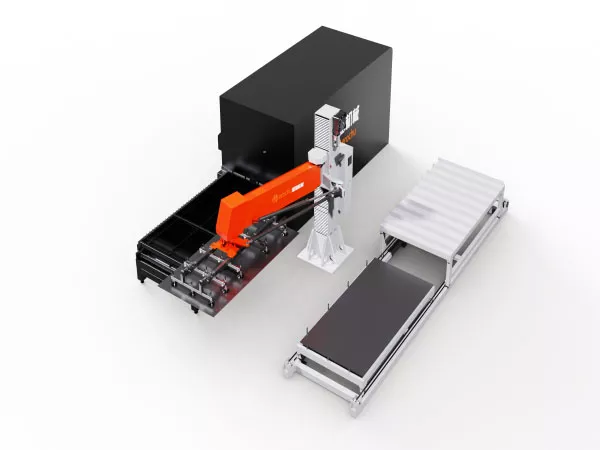
What is a Cantilever Manipulator for Laser Cutting?
A cantilever manipulator, also known as a laser cutting loading machine, is an automated material handling system that feeds raw sheets into laser cutting machines with extreme precision. Unlike traditional manual loading methods, this robotic system ensures:
- Faster material transfer
- Higher positioning accuracy
- Reduced human intervention
- 24/7 operational capability
Key Components & Working Principle
The system consists of:
- Robotic arm with cantilever design (for extended reach)
- Gripping mechanism (mechanical, pneumatic, or vacuum-based)
- Precision positioning sensors
- PLC control system (for automated operation)
It operates by:
- Automatically detecting sheet metal dimensions
- Securely gripping the material
- Transporting it to the laser cutting bed
- Precisely aligning for optimal cutting
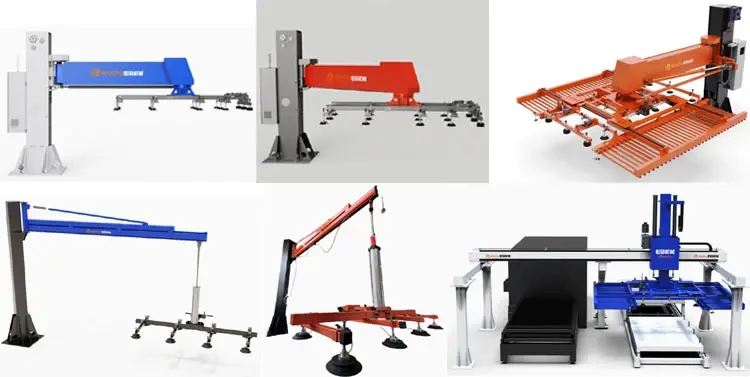
How Does a Laser Cutting Loading Machine Work?
1. Material Identification & Handling
The system uses advanced sensors and vision systems to:
- Detect sheet position, size, and shape
- Adjust gripping force based on material thickness
- Prevent slippage during transportation
2. Material Transportation Methods
Three primary technologies are employed:
A. Mechanical Gripping
- Uses clamps or forks for secure holding
- Ideal for thicker materials (3mm+)
- Most cost-effective solution
B. Pneumatic Systems
- Employs air pressure-controlled grippers
- Suitable for delicate surfaces
- Allows adjustable gripping force
C. Vacuum Adsorption
- Uses suction cups for flat sheets
- Perfect for thin, polished materials
- Prevents surface scratches
3. Precision Positioning
Once transported, the system:
- Aligns materials within ±0.1mm accuracy
- Adjusts for laser cutting bed coordinates
- Ensures optimal nesting for minimal material waste
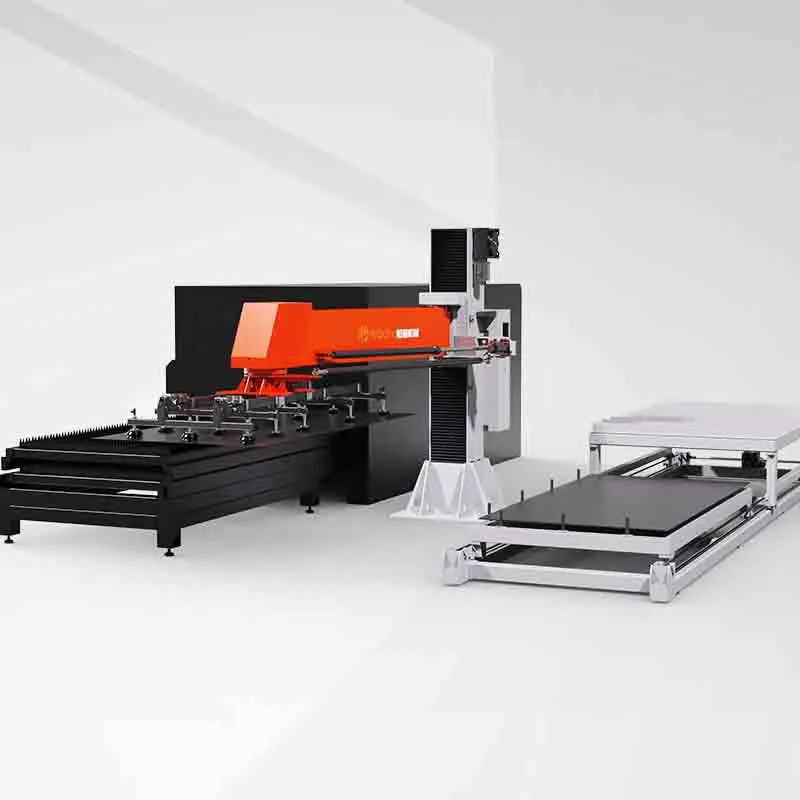
Benefits of Automated Laser Cutting Loading Systems
1. Increased Productivity
- 30-50% faster than manual loading
- Enables lights-out manufacturing
- Processes more sheets per hour
2. Enhanced Precision
- Eliminates human measurement errors
- Consistent cutting quality
- Perfect for high-tolerance parts
3. Cost Reduction
- Lower labor costs (fewer operators needed)
- Reduced material waste (optimal nesting)
- Minimized machine idle time
4. Improved Safety
- Removes workers from hazardous zones
- Prevents lifting injuries
- Complies with OSHA automation standards
Technical Specifications & Customization Options
Parameter | Specifications |
---|---|
Loading Capacity | 150kg – 2000kg |
Positioning Accuracy | ±0.1mm |
Sheet Thickness | 0.5mm – 25mm |
Gripping Methods | Mechanical/Pneumatic/Vacuum |
Control System | PLC with HMI interface |
Integration | Compatible with major laser brands |
Customization Features
- Expandable reach for large-format sheets
- AI-powered vision systems for mixed-material handling
- IoT connectivity for smart factory integration
Industry Applications
1. Automotive Manufacturing
- Body panels, chassis components
- High-volume production with consistent quality
2. Aerospace Industry
- Aircraft structural parts
- Titanium and aluminum sheet handling
3. Electronics Enclosures
- Server racks, control boxes
- Precision handling of thin gauge metals
4. Construction & Architecture
- Metal facades, decorative elements
- Heavy-duty steel plate manipulation
Future Trends in Laser Cutting Automation
The next generation of cantilever manipulators will feature:
- Machine learning algorithms for self-optimization
- Collaborative robotics (cobots) for hybrid operations
- Predictive maintenance through IoT sensors
- Green manufacturing capabilities (energy recovery systems)
Conclusion: Why Invest in Automated Loading?
The cantilever manipulator for laser cutting represents the future of smart manufacturing, offering:
✔ Unmatched efficiency in material handling
✔ Superior cut quality through precise positioning
✔ Significant cost savings via automation
✔ Future-ready technology for Industry 4.0
For manufacturers looking to boost productivity while reducing operational costs, this automated loading system delivers immediate ROI and long-term competitive advantage.
Upgrade your laser cutting operation today with robotic automation!