In the era of smart manufacturing, automatic sheet metal storage systems have emerged as a cornerstone of efficient warehouse operations. Designed as advanced automatic storage and retrieval systems (AS/RS) for sheet metal, these racks redefine how industries handle, store, and retrieve flat materials. By leveraging vertical warehouse space and adopting a Goods-to-Operator workflow, they eliminate manual material handling bottlenecks, making them indispensable for modern factories, fabrication shops, and distribution centers.
How Automatic Sheet Metal Storage Works
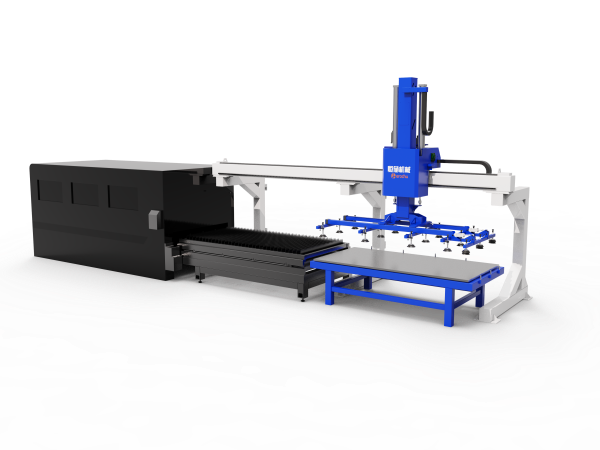
At its core, an automatic sheet metal storage rack operates on a simple yet powerful principle: bringing materials directly to the worker, rather than requiring workers to search for materials. The system integrates with a lifter mechanism that precisely deposits and retrieves drawers—each holding sheets, moulds, boxes, or components—and delivers them to a loading/unloading bay at a safe, ergonomic height. This seamless process minimizes worker movement, reduces fatigue, and speeds up material access.
Unlike traditional storage solutions, which rely on manual labor to navigate cluttered shelves, automatic systems use intelligent controls to manage inventory. Workers interact with a touch screen interface to request specific materials, and the system’s lifter springs into action, locating the correct drawer and positioning it for easy access. This automation ensures that even large or heavy sheets are handled with precision, eliminating the risk of human error.
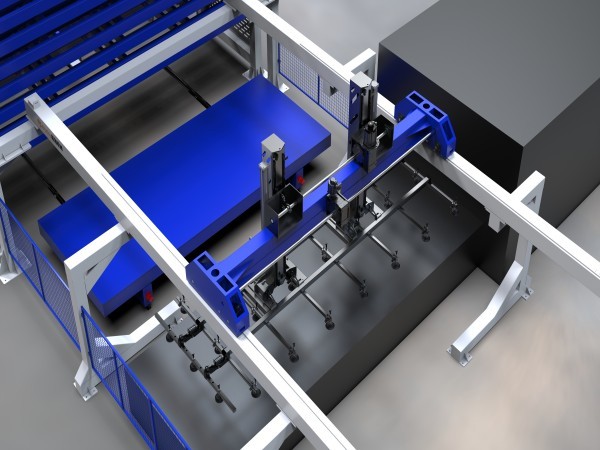
Key Features: Why Automatic Storage Stands Out
- Space Optimization: By maximizing vertical storage, these systems drastically reduce the floor footprint required for material storage. This is a game-changer for facilities with limited space, allowing them to store more materials without expanding their premises.
- Cost Reduction: Lower material handling costs are a direct benefit. With automation taking over repetitive tasks, labor expenses decrease, and productivity rises. Fewer man-hours spent on retrieving materials mean more time allocated to value-added production activities.
- Efficient Material Flow: The system streamlines inventory movement, ensuring materials are stored and retrieved in the shortest possible time. This efficiency translates to faster production cycles, helping businesses meet tight deadlines.
- Enhanced Safety: Safety is prioritized with features that protect both workers and materials. By eliminating the need for climbing, reaching, or manually lifting heavy sheets, the risk of injuries is significantly reduced. Additionally, materials are stored securely in drawers, preventing damage from collisions or improper stacking.
- Real-Time Inventory Tracking: The system provides updated inventory status, giving managers accurate data on stock levels, usage patterns, and material locations. This visibility helps prevent stockouts, reduce overstocking, and optimize procurement.
- Heavy-Duty Capacity: Built to handle industrial demands, each drawer supports a standard load of 3 tons (with a maximum capacity of 5 tons). This robustness makes the system suitable for thick steel sheets, heavy moulds, and other large components.
- User-Friendly Controls: The touch screen control system simplifies operation, requiring minimal training for workers. Intuitive menus allow for quick material requests, and the interface provides real-time feedback on system status, ensuring smooth operation.
Customization and Configuration Options
Automatic sheet metal storage systems are highly customizable, designed to accommodate a variety of materials beyond sheet metal, including moulds, boxes, and components. The Constant Storage Configuration Table (Board Class) for drawer-type tray storage shelves offers standardized models with flexible parameters:
- Model Range: Popular models like HC-B3015-63, HC-B4015-63, HC-B4020-65, and HC-B6020-66 cater to different sheet sizes, from 3000x1500mm to 6000x2000mm.
- Load Capacity: Single-layer loads range from 3 tons (HC-B3015-63, HC-B4015-63) to 6 tons (HC-B6020-66), with customization available for heavier needs.
- Layer Configuration: Most models feature 5+1 layers (6 layers total), with each partition layer offering up to 220mm of height, adapting to various material thicknesses.
- Dimensions: External dimensions vary by model, from 3505x2280x2000mm (HC-B3015-63) to 6505x2280x2500mm (HC-B6020-66), ensuring compatibility with different warehouse layouts. Even device colors can be customized to match facility aesthetics.
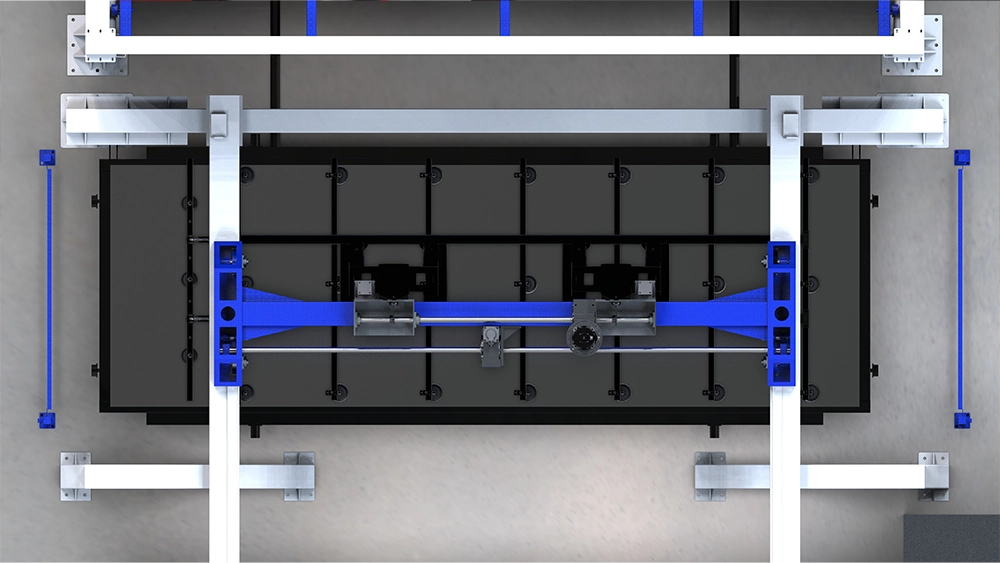
Applications Across Industries
Automatic sheet metal storage systems are versatile enough to serve diverse sectors:
- Metal Fabrication: Quickly access steel or aluminum sheets for cutting, bending, or welding, reducing setup time between production steps.
- Automotive Manufacturing: Store large car body panels or components, ensuring assembly lines have a steady supply of materials.
- Aerospace: Safely store delicate or high-value materials, such as titanium sheets, with precise handling to maintain quality.
- Mould and Die Production: Organize heavy moulds and tooling, making them easily accessible for maintenance or production runs.
Conclusion: Investing in the Future of Storage
An automatic sheet metal storage system is more than a storage solution—it’s an investment in operational efficiency, safety, and scalability. By automating material handling, businesses reduce costs, minimize errors, and create a more productive work environment. With customizable configurations, heavy-duty capacity, and user-friendly controls, these systems adapt to evolving industrial needs, ensuring long-term value.
For facilities looking to stay competitive in a fast-paced market, switching to automatic storage isn’t just an upgrade—it’s a strategic move that transforms how materials are managed, from storage to production. Embrace the future of industrial storage with a system that delivers speed, safety, and savings, all at the touch of a screen.