In the fast-paced world of modern manufacturing and warehousing, the demand for streamlined operations, cost reduction, and enhanced safety has never been higher. Enter the automatic loading and unloading system — a technological marvel that is transforming industries by automating one of the most labor-intensive and time-consuming aspects of production and logistics. At the heart of this system lies a synergy of advanced components, with laser loading and unloading robots taking center stage, working in harmony with other key elements to deliver unprecedented efficiency.
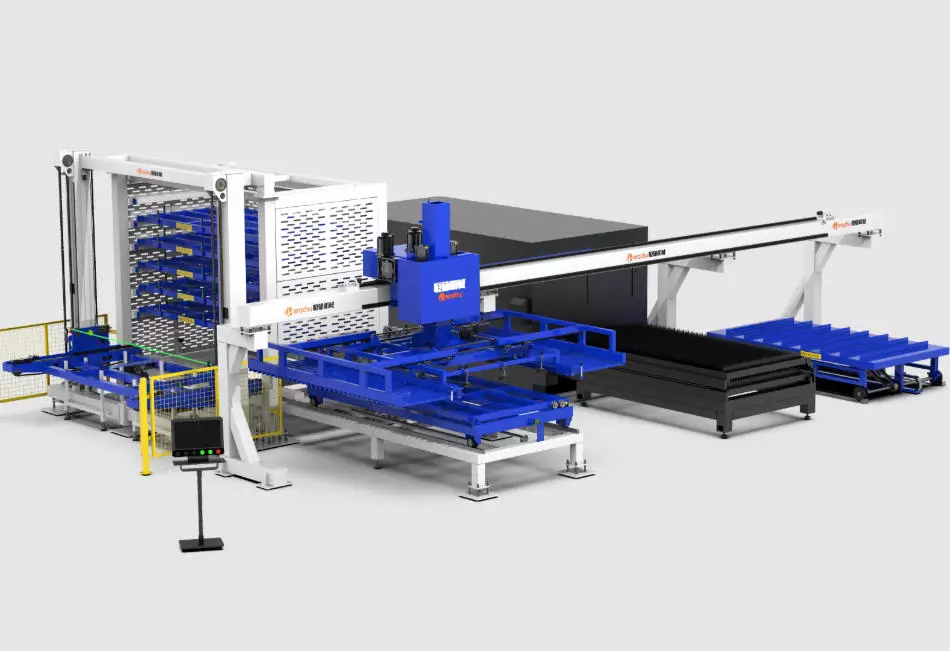
Laser loading and unloading robots are not just ordinary machines; they are precision-engineered workhorses designed to redefine productivity. By taking over the task of automatic loading and unloading, these robots eliminate the need for manual intervention, which is often prone to errors, delays, and safety risks. What sets them apart is their ability to achieve more economical production. Manual labor comes with ongoing costs such as salaries, benefits, and training, not to mention the potential for human error that can lead to material waste or damaged goods. Laser robots, on the other hand, operate with consistent precision, reducing material waste and minimizing the likelihood of costly mistakes. Over time, this translates into significant cost savings for businesses, making the initial investment in these systems a wise long-term decision.
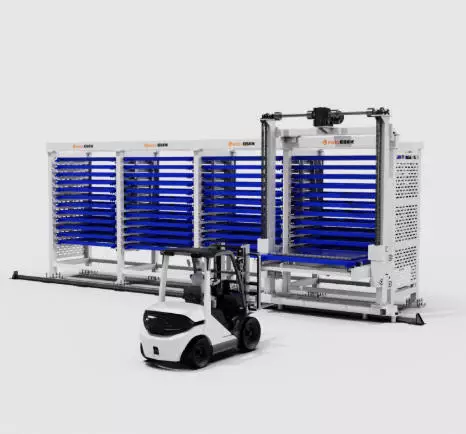
Safety is another critical area where laser loading and unloading robots shine. Industrial environments, especially those involving heavy machinery like laser cutting machines, can be hazardous for human workers. Accidents related to material handling, such as lifting heavy objects or working in close proximity to moving parts, are common in manual operations. Laser robots are equipped with advanced sensors and safety protocols that allow them to navigate their surroundings with caution, avoiding collisions with other equipment or workers. This not only protects employees from harm but also reduces the number of workplace accidents, which can result in costly downtime, legal issues, and damage to a company’s reputation.
The loading and unloading device, a key component of the system, forms the most compact automation unit of the warehousing system through the use of linear axes. Linear axes are mechanical components that enable precise linear movement, allowing the device to position itself with incredible accuracy. This compact design is a game-changer for facilities with limited space. Traditional loading and unloading setups often require large areas to accommodate manual labor or bulky machinery, but the linear axis-based system maximizes space utilization, making it suitable for small to medium-sized warehouses and production plants.
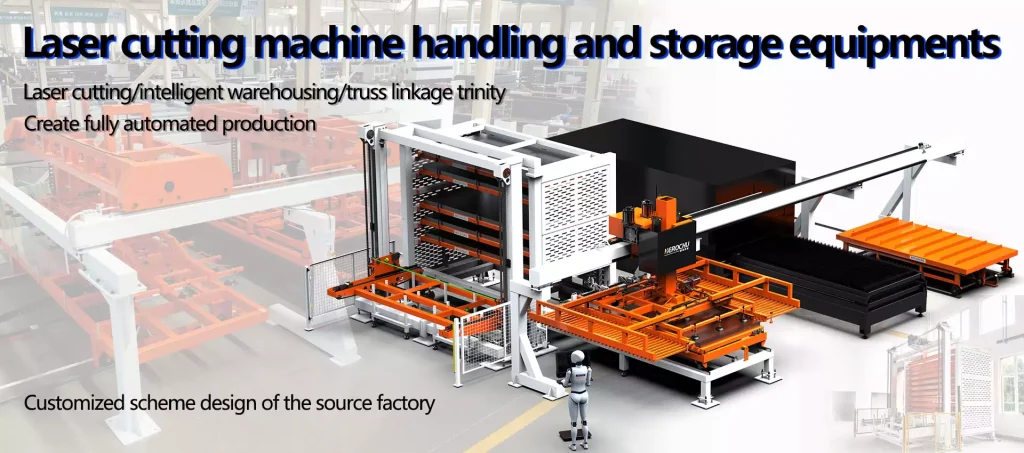
To fully understand the power of the automatic loading and unloading system, it’s essential to look at its three main components: the laser cutting machine, the laser loading and unloading robot, and the electric exchange trolley. Each plays a unique role, and their integration creates a seamless workflow that boosts productivity from start to finish.
The laser cutting machine is the workhorse of the production process, capable of cutting through a variety of materials — from metal sheets to plastics — with unmatched precision and speed. However, its efficiency is only as good as the loading and unloading process that feeds it. This is where the laser loading and unloading robot steps in. The robot works in tandem with the laser cutting machine, automatically feeding raw materials into the machine and removing the finished products once the cutting process is complete. This continuous flow ensures that the laser cutting machine operates at maximum capacity, minimizing idle time and increasing overall output.
Complementing the robot and the laser cutting machine is the electric exchange trolley. This component is responsible for transporting materials between different stages of the production line or between storage areas and the cutting machine. The trolley is electrically powered, making it eco-friendly and cost-effective to operate. It can be programmed to follow specific routes, ensuring that materials are delivered to the right place at the right time. The electric exchange trolley also enhances safety by reducing the need for manual material transport, which often involves heavy lifting and the use of forklifts — a common source of workplace accidents.
One of the greatest advantages of this integrated system is its flexibility. It can be easily customized to meet the specific needs of different industries. For example, in the automotive industry, where precision and speed are paramount, the system can be programmed to handle large metal sheets used in car body manufacturing. In the electronics industry, it can be adjusted to work with smaller, more delicate components, ensuring that they are handled with care to avoid damage. This adaptability makes the automatic loading and unloading system a valuable asset for a wide range of applications.
Another benefit is the data-driven insights that the system provides. Many modern automatic loading and unloading systems are equipped with sensors and software that collect real-time data on performance metrics such as production speed, material usage, and machine downtime. This data can be analyzed to identify bottlenecks in the process, optimize workflows, and make informed decisions about maintenance and resource allocation. For instance, if the data shows that the laser cutting machine is frequently idle waiting for materials, adjustments can be made to the robot’s programming or the trolley’s route to ensure a more steady supply of raw materials.
In conclusion, the automatic loading and unloading system, with its laser loading and unloading robots, linear axis-based compact design, and integration of laser cutting machines and electric exchange trolleys, is revolutionizing industrial operations. It offers a winning combination of economy, safety, and efficiency, helping businesses reduce costs, protect their workforce, and increase productivity. As technology continues to advance, we can expect these systems to become even more sophisticated, further pushing the boundaries of what’s possible in manufacturing and warehousing. For any business looking to stay competitive in today’s market, investing in an automatic loading and unloading system is not just an option — it’s a necessity.